6s中的八大浪费是:缺陷、过量生产、等待、运输、库存、动作、未充分利用人员、未充分利用设备。
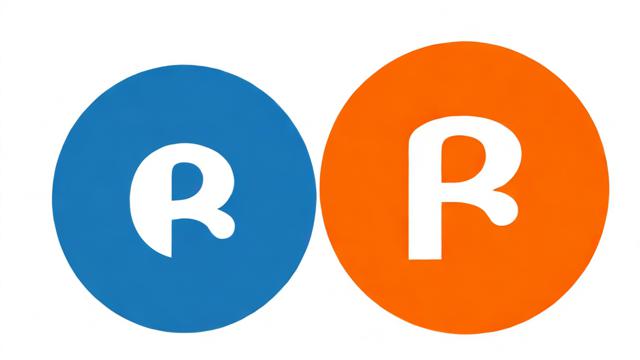
在6S管理法中,八大浪费是指企业在生产、运营和管理过程中常见的八种资源浪费现象,以下是对这八大浪费的详细解释:
1. 过量生产的浪费(Overproduction)
定义:过量生产是指生产出超过需求的产品,这不仅占用了生产资源,还可能导致库存积压和资金浪费。
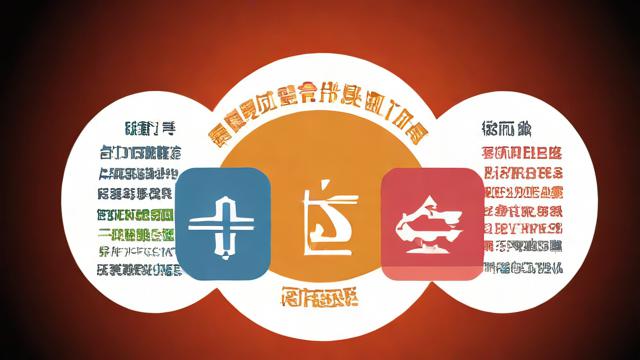
影响:
增加库存成本
导致产品过时或损坏
掩盖生产过程中的问题
改进措施:实施准时化生产(JIT),确保按需生产,减少库存。
等待的浪费(Waiting)
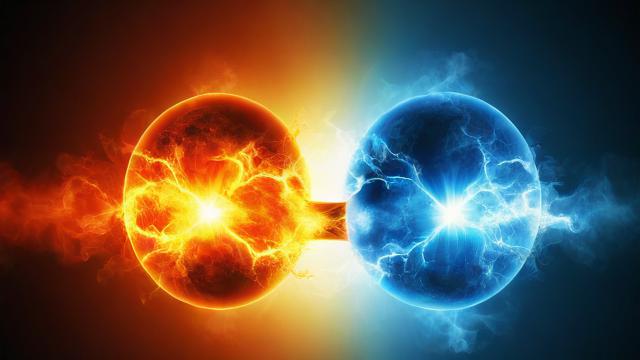
定义:等待是指在生产过程中,由于机器故障、物料短缺或人员不足等原因导致的生产停滞。
影响:
降低生产效率
增加生产成本
延长交货周期
改进措施:优化生产流程,提高设备维护效率,确保物料和人员的充足供应。
3. 运输的浪费(Transportation)
定义:运输浪费是指在生产过程中,不必要的物料搬运和移动。
影响:
增加运输成本
延长生产周期
可能导致物料损坏或丢失
改进措施:优化工厂布局,减少物料搬运距离,采用高效的物流系统。
4. 过度加工的浪费(Over-processing)
定义:过度加工是指对产品进行超出客户需求的加工或处理。
影响:
增加生产成本
降低生产效率
可能影响产品质量
改进措施:与客户沟通,了解其真实需求,避免不必要的加工步骤。
库存的浪费(Inventory)
定义:库存浪费是指过多的原材料、在制品或成品库存。
影响:
占用大量资金
增加仓储成本
可能导致物料过期或损坏
改进措施:实施精益库存管理,如看板管理,减少库存水平。
动作的浪费(Motion)
定义:动作浪费是指员工在生产过程中进行不必要的动作或移动。
影响:
降低生产效率
增加员工疲劳度
可能影响产品质量
改进措施:通过工作分析和流程优化,减少不必要的动作和移动。
不良品的浪费(Defects)
定义:不良品浪费是指由于生产过程中的错误或缺陷导致的废品或返工。
影响:
增加生产成本
降低生产效率
损害公司声誉
改进措施:加强质量控制,提高员工技能和意识,减少不良品产生。
8. 潜能未被利用的浪费(Underutilized Talent)
定义:潜能未被利用的浪费是指员工的技能和创造力没有得到充分发挥。
影响:
降低员工满意度和忠诚度
限制企业创新能力和发展
浪费人力资源
改进措施:提供培训和发展机会,鼓励员工参与决策和创新活动。
相关问答FAQs
Q1: 如何识别并减少生产过程中的浪费?
A1: 进行全面的生产流程分析,找出存在的浪费点,根据具体的浪费类型,采取相应的改进措施,如优化生产流程、提高设备维护效率、加强质量控制等,持续监控和评估改进效果,确保浪费得到有效控制。
Q2: 6S管理法中的八大浪费与企业绩效有何关联?
A2: 6S管理法中的八大浪费直接影响企业绩效,通过识别并减少这些浪费,企业可以提高生产效率、降低成本、提升产品质量和客户满意度,从而增强市场竞争力,减少浪费还有助于释放企业资源,促进创新和发展。
小编有话说:
6S管理法中的八大浪费是企业管理中不可忽视的重要问题,通过深入理解和有效应对这些浪费,企业可以显著提升运营效率和市场竞争力,希望本文能为您提供有益的参考和启示,助您在企业管理的道路上不断前行。