做不好6S管理的原因可能是:缺乏全员参与、培训不足、标准不明确、监督不到位及奖惩机制不完善。
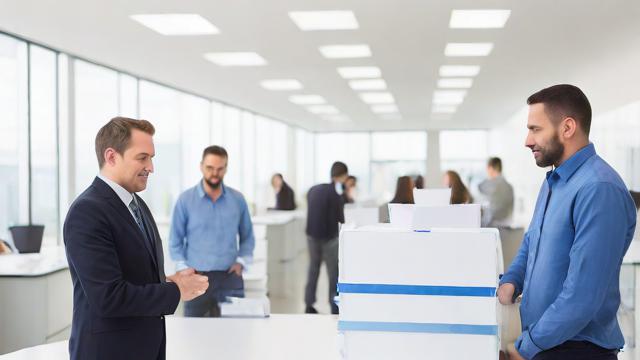
我们做不好6S管理的原因主要有以下几方面:
一、认识层面不足
1、理解偏差:许多企业将6S简单理解为大扫除,未意识到其最终目标是提升员工品质以及整体管理水平,这种片面的理解导致在实施过程中只注重表面形式的清洁,而忽略了6S管理对于员工素养提升、工作流程优化等深层次的意义。
2、认知局限:部分基层员工甚至中高层管理者对6S的认识也不到位,有人认为生产任务重就没时间开展6S活动,将6S与生产对立起来;还有些基层人员认为6S管理只是搞卫生,没有认识到其在建立完善管理系统、提高生产效率等方面的重要性。
二、实施方案问题
1、脱离实际:很多企业的6S实施方案就像一个通用的管理文本,流于表面化和形式化,与企业的具体情况差距较大,缺乏针对性和可操作性,一些企业在制定6S标准时,没有充分考虑自身场地、设备、人员素质等实际情况,导致标准过高或过低,难以有效执行。
2、缺乏创新:部分企业的6S实施方案多年不变,未能与时俱进,对6S的最新发展和创新方法不了解,仍然按照传统的模式进行管理,无法适应企业发展的需求。
三、执行力欠缺
1、领导支持不足:领导对6S管理的支持力度不够,在实施过程中未能给予足够的资源保障和政策支持,一些领导自身对6S管理的认识不够深刻,没有将其作为企业管理的重要组成部分来抓,导致6S管理工作在企业中得不到高度重视。
2、员工积极性不高:员工对6S管理的认识不足,缺乏参与的积极性和主动性,由于宣传不到位,员工对6S管理的内容和意义了解不够;企业在推行6S管理时,未能充分调动员工的积极性,让员工感受到6S管理带来的好处,导致员工在执行过程中敷衍了事。
3、监督检查不力:企业缺乏有效的监督检查机制,对6S管理的执行情况监督不到位,在实施过程中,存在实际行动与实施方案脱节、不认真执行规定等问题,导致6S管理工作难以落到实处。
四、资源限制因素
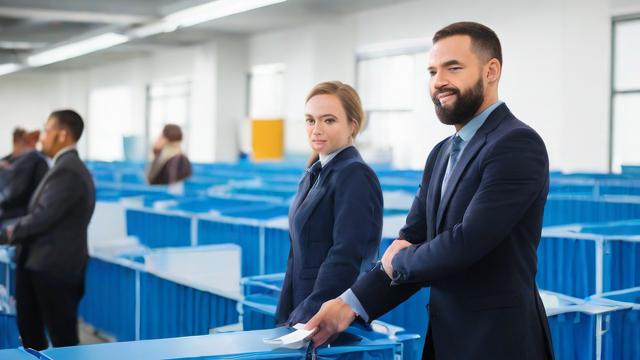
1、场地有限:随着企业的发展,设备、物料等不断增加,但场地却没有相应扩充,导致物品摆放混乱,无法按照6S管理的要求进行合理的规划和布局,一些工厂十年前是一幢厂房,十年后设备增加了,产线增加了,还是一幢楼,产品堆积如山,通道拥堵,严重影响了6S管理的实施。
2、资金不足:6S管理的推行需要一定的资金支持,如购买相关的工具、设备,进行培训等,如果企业资金紧张,无法满足这些需求,就会影响6S管理的实施效果,一些企业想要制作高质量的6S标识牌,但由于资金有限,只能选择质量较差的材料,不仅影响美观,还容易损坏。
五、企业文化影响
1、短期行为思维:不少企业期望通过一场运动式的活动来快速改变现场脏乱差及人员素养低下的状况,缺乏长期坚持的决心和耐心,在推行6S管理时,容易出现“一紧二松三垮台四重来”的局面,导致6S管理无法持续有效地推进。
2、传统观念束缚:一些企业的传统观念根深蒂固,认为建筑工地就是脏、乱的地方,堆放建筑垃圾是正常的现象,不必及时清扫,这种观念在一定程度上影响了员工对6S管理的认可和执行,使得6S管理工作难以深入开展。
六、激励机制缺失
1、激励措施不足:企业缺乏长效的激励机制,未能将6S管理与员工的切身利益挂钩,员工在推行6S管理过程中,看不到明显的利益回报,导致其参与的积极性不高,一些企业在考核评价中,对6S管理的考核权重较低,或者没有相应的奖励措施,无法激发员工的工作热情。
总的来看,企业做不好6S管理的原因是多方面的,包括认识层面的不足、实施方案的问题、执行力的欠缺、资源的限制、企业文化的影响以及激励机制的缺失等,要想做好6S管理,企业需要从多个方面入手,提高全员对6S管理的认识和理解,制定符合企业实际情况的实施方案,加强执行力建设,提供必要的资源支持,营造良好的企业文化氛围,并建立健全激励机制,确保6S管理能够持续有效地推进。