车间 5S 工作没做好,可能是标准不明确、监督不到位、员工意识不足或未持续改进。
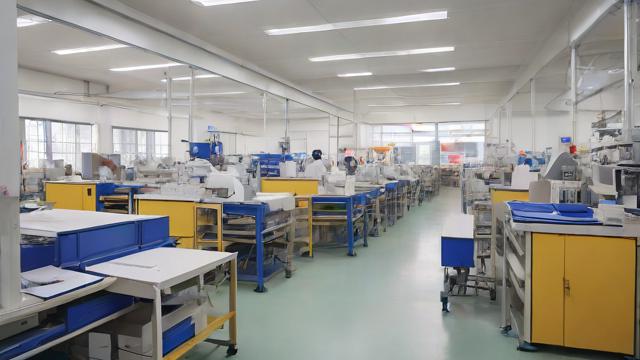
车间工作5S工作为什么没做好
在现代企业的车间管理中,5S工作(整理、整顿、清扫、清洁、素养)是提升工作效率、保障产品质量、优化工作环境以及培养员工良好工作习惯的重要管理方法,在实际的车间工作中,5S工作常常未能达到预期效果,存在诸多问题,以下是对车间工作5S工作没做好的原因的详细分析:
一、人员意识方面
原因类别 | 具体表现 | 影响 |
缺乏重视 | 部分车间管理人员和员工对5S工作的理解仅仅停留在表面,没有充分认识到其对于车间生产效率、产品质量和员工安全的重要性,他们可能更关注生产任务的完成,而将5S工作视为额外的负担,认为其对生产没有直接的帮助,从而在思想上不够重视,缺乏积极主动推行5S工作的意愿。 | 导致5S工作在车间难以得到有效开展,各项措施无法真正落实,车间环境依旧脏乱差,物品摆放杂乱无章,影响工作效率和员工的工作积极性。 |
培训不足 | 企业虽然开展了5S培训,但培训内容可能过于理论化,缺乏与车间实际工作情况相结合的案例和操作指导,培训方式也可能较为单一,如单纯的集中授课,员工参与度不高,难以理解和掌握5S的精髓和实际操作方法,培训频率较低,不能及时强化员工对5S工作的认识和技能,导致员工在实际工作中不知道如何正确进行整理、整顿等操作。 | 员工对5S工作的理解存在偏差,执行过程中出现不规范的行为,在整理环节,不清楚哪些物品是真正需要保留的,哪些是可以丢弃的;在整顿环节,不会合理规划物品的存放位置和标识方法,使得工作现场仍然混乱,无法达到5S工作要求的有序状态。 |
二、制度执行方面
原因类别 | 具体表现 | 影响 |
制度不完善 | 企业制定的5S管理制度可能存在漏洞和缺陷,例如对5S工作的标准和要求规定不够明确细致,导致员工在执行过程中缺乏统一的依据,对于不同区域、不同设备、不同物料的整理、整顿标准没有具体的量化指标,使得员工在操作时感到困惑,不知道要达到什么样的程度才算符合5S要求,制度中可能缺乏对违反5S规定的行为的相应处罚措施,或者处罚力度较轻,难以起到威慑作用。 | 5S工作在车间无法实现标准化和规范化,员工各自为政,工作质量和效果参差不齐,由于缺乏明确的处罚机制,一些员工即使不遵守5S规定,也不会受到应有的惩罚,从而影响了其他员工的积极性,导致整个车间的5S工作陷入恶性循环。 |
执行不严格 | 即使有完善的5S制度,但在执行过程中往往大打折扣,车间管理人员可能因为忙于生产任务,对5S工作的监督检查流于形式,不能及时发现和纠正员工的违规行为,对于发现的问题,没有及时采取有效的整改措施,而是听之任之,导致问题不断积累和恶化,在执行制度时可能存在人情因素,对一些员工的违规行为网开一面,没有做到公平公正地执行制度,破坏了制度的严肃性。 | 5S工作无法持续有效地推进,车间环境很快又会回到原来的脏乱差状态,员工也会因为制度的执行不严格而逐渐失去对5S工作的信任和重视,认为5S工作只是走过场,从而不再积极配合5S工作的开展。 |
三、资源投入方面
原因类别 | 具体表现 | 影响 |
人力不足 | 车间人员配备紧张,员工除了要完成繁重的生产任务外,还要兼顾5S工作,导致精力分散,没有足够的时间和精力去认真开展5S活动,在清扫环节,由于人员不足,可能无法及时清理工作现场的垃圾和杂物,影响车间的整洁度;在整顿环节,也没有专人负责规划物品的摆放和标识,使得物品管理混乱。 | 5S工作只能勉强应付,无法达到预期的效果,长期的人力不足还会导致员工疲劳作业,增加安全隐患,同时也会影响员工的工作效率和工作质量,进而影响整个车间的生产效益。 |
资金有限 | 企业在5S工作方面的资金投入不足,无法为车间提供足够的5S工具和设备,如合适的收纳容器、清洁用品、标识牌等,缺乏这些必要的资源,员工在进行整理、整顿和清扫工作时会受到很大的限制,难以有效地开展5S活动,没有足够数量和规格的收纳容器来分类存放工具和物料,就会导致工具和物料随意堆放,影响工作效率和车间的整洁度。 | 5S工作难以顺利开展,无法为员工创造良好的工作环境和工作条件,有限的资金投入也可能影响企业对车间环境的改善和优化,如无法及时维修损坏的设备、更新老化的设施等,进一步制约了5S工作的实施效果。 |
四、考核激励方面
原因类别 | 具体表现 | 影响 |
考核体系不合理 | 企业建立的5S考核体系可能过于注重表面的检查和短期的效果,而忽视了对5S工作过程的监督和长期效果的评估,考核指标可能单一且不全面,只关注车间的整洁度和物品摆放是否整齐等外在表现,而对于员工在5S工作中的参与度、团队协作精神以及对5S理念的贯彻执行等方面缺乏有效的考核,这种不合理的考核体系不能真实反映车间5S工作的实际水平和员工的工作情况,容易导致员工为了应付考核而采取一些临时性的措施,而不是真正将5S工作融入到日常工作中。 | 员工为了在考核中取得好成绩,可能会在检查前突击进行5S整理,而在平时则依然我行我素,不注重日常的5S维护,这样不仅无法真正提高车间的5S管理水平,还会浪费企业的资源和时间,同时也不利于培养员工的良好的工作习惯和责任感。 |
五、持续改进方面
原因类别 | 具体表现 | 影响 |
缺乏反馈机制 | 车间在5S工作实施过程中,没有建立起有效的反馈机制,员工无法及时将自己在工作中遇到的问题、困难以及对5S工作的意见和建议反馈给管理层,管理层也难以了解5S工作在基层的实际执行情况和员工的心声,导致信息沟通不畅,问题无法得到及时解决,员工可能在整理过程中发现某些工具没有合适的存放位置,但由于缺乏反馈渠道,这个问题一直得不到解决,影响了整理工作的效果。 | 5S工作中出现的问题会不断积累,逐渐成为制约5S工作深入开展的瓶颈,员工的积极性也会因为问题得不到解决而受到打击,对5S工作的认同感和参与度降低,最终影响5S工作的持续推进和整体效果。 |
六、外部环境方面
原因类别 | 具体表现 | 影响 |
生产任务紧迫 | 当车间面临大量的生产订单和紧迫的生产任务时,为了满足交货期的要求,车间管理人员和员工往往会将大部分精力都放在生产上,而无暇顾及5S工作,在这种情况下,5S工作会被暂时搁置一旁,工作现场的物品摆放会变得杂乱无序,环境卫生也会变差,在赶制一批紧急订单时,原材料可能会随意堆放在过道上,工具使用后也不能及时归位,导致车间一片混乱。 | 5S工作受到严重冲击,前期的工作成果可能会毁于一旦,而且在这种混乱的工作环境下,更容易引发安全事故和质量问题,反过来又会影响生产任务的顺利完成,形成恶性循环。 |
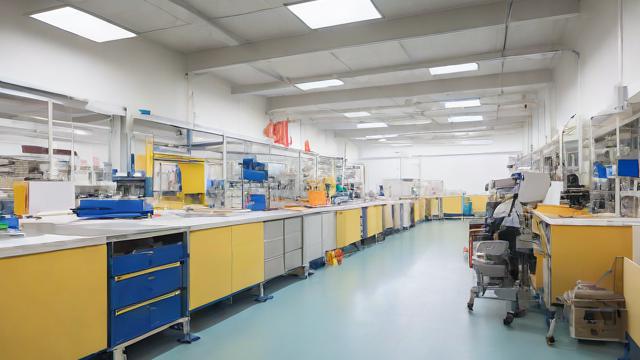
相关问答FAQs
问题1:如何提高员工对5S工作的重视程度?
答:可以通过加强培训教育,向员工详细讲解5S工作的重要性和意义,结合车间实际情况列举因5S工作不到位而导致的生产效率低下、质量问题等案例,让员工切实感受到5S工作与自身利益息息相关,设立奖励机制,对在5S工作中表现优秀的员工给予物质和精神奖励,激发员工的积极性和主动性,车间管理人员要以身作则,带头做好5S工作,为员工树立榜样。
问题2:怎样确保5S制度能够严格执行?
答:首先要完善5S制度,明确各项工作的标准和要求,制定详细的操作流程和量化指标,使员工清楚知道该怎么做以及做到什么程度,加强对制度执行情况的监督检查,建立定期检查和不定期抽查相结合的机制,及时发现问题并督促整改,对于违反制度的行为,要严格按照规定进行处罚,做到公平公正,维护制度的严肃性,将5S工作的执行情况纳入绩效考核体系,与员工的薪酬、晋升等挂钩,促使员工自觉遵守制度。
小编有话说
车间工作5S工作没做好是由多方面原因造成的,要想改变这种现状,企业需要从人员意识、制度执行、资源投入、考核激励、持续改进以及外部环境等多个维度入手,全面系统地解决问题,只有持之以恒地推进5S工作,才能真正提升车间的管理水平,为企业的发展奠定坚实的基础。