5S管理中的安全指的是在整理、整顿、清扫、清洁和素养各环节中确保员工操作与环境无安全隐患。
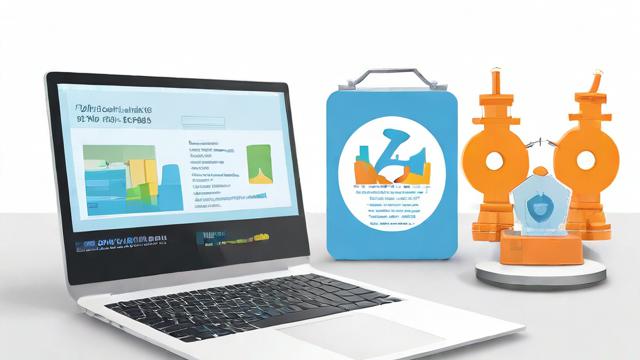
5S管理中虽然没有明确单独提出“安全”这一要素,但每个环节都与安全息息相关,其对安全的保障贯穿于整个管理过程,以下是详细分析:
1、整理中的安全:整理即区分要与不要的物品,将不要的物品处理掉,当工作场所清爽起来时,安全性也大为增加,私拉乱接、用途不清、一片混乱的情况大为减少,从而降低了员工因环境杂乱而发生意外的风险,比如在一些工厂中,如果工作区域堆满了不必要的杂物,员工在行走或操作过程中就很容易绊倒或碰撞到物品,导致受伤,而通过整理,清除这些杂物,能够使工作场所更加整洁有序,为员工提供更安全的工作环境。
2、整顿中的安全:整顿即划分区域,并用三定原则(定点、定容、定量)对物品进行定置管理,合格品区、待检区、作业区以及危险(品)的标识,有助于提醒人们勿要乱走乱闯,例如在铸件车间,立上一块铭牌,上面写着:“高温区域,非工作人员,请勿靠近!”一般人等将不会误闯其中,而三定原则的运用更是对危险的进一步防范,在三定原则下,物品都有严格的标识与放置规定,误用的几率几乎为零,比如在仓库中,将易燃、易爆、有毒等危险物品按照规定的位置和容量存放,并做好明确的标识,可以有效避免因物品存放不当而引发的安全事故。
3、清扫中的安全:清扫中有三扫,分别是扫黑、扫漏、扫怪,清扫不仅是扫除脏污,同时也是扫除漏水漏电漏气以及各种异常状况,清扫在扫除脏污的基础上进行点检,发现各种微缺陷和异常状况,做好这一点,可以说基本扫除了各种危险源,这是清扫在安全管理方面的重要作用,定期清扫设备表面的灰尘和油污,不仅可以保持设备的正常运行,还能及时发现设备的磨损、松动等问题,提前进行维修和更换,防止因设备故障引发的安全事故。
4、清洁中的安全:清洁意味着制度化与规范化,订立各种细致的制度与标准,这当中就包括危险源的识别以及各种安全规范,通过建立清洁的标准和流程,确保工作场所的干净整洁,减少因环境不卫生而导致的疾病传播和安全隐患,在食品加工企业中,严格按照清洁管理制度对生产车间进行清洁消毒,可以防止细菌滋生,保证食品的安全;在电子厂中,保持工作场所的清洁可以减少静电的产生,降低因静电引发的火灾和爆炸风险。
5、素养中的安全:素养是一种习惯与自律,形成人人相互关爱的工作氛围,通过长期训练,员工乐意遵守各项包括安全要求在内的规范,共同营造一个安全、人性化与高效的作业环境,员工的素养提高了,就会自觉遵守安全规章制度,减少违规操作行为,从而降低事故发生的可能性,新员工入职时进行安全知识和操作规程的培训,让员工养成良好的工作习惯和安全意识,在工作中时刻注意自身和他人的安全。
5S管理要素 | 与安全相关的体现 | 具体示例 |
整理 | 清除杂物,减少混乱,降低意外风险 | 清理工作区域通道中的障碍物,防止绊倒 |
整顿 | 区域划分,物品定置,避免危险 | 设置危险区域警示标识,防止误闯 |
清扫 | 扫除异常状况,点检隐患 | 定期检查设备,及时修复故障 |
清洁 | 订立制度标准,识别危险源 | 制定清洁标准,防止细菌滋生引发安全问题 |
素养 | 培养安全意识和习惯 | 员工自觉遵守安全规定,减少事故 |
相关问答FAQs
问题1:5S管理中哪个环节最能直接体现安全?
回答:在5S管理中,整顿环节可能最能直接体现安全,因为整顿通过划分区域、标识危险区域以及物品的定置管理,能够直观地提醒人们注意安全,避免进入危险区域或因物品摆放不当而导致的事故,在工厂车间设置明显的“高温危险”“禁止靠近”等标识,让人们一眼就能看到并引起警觉。
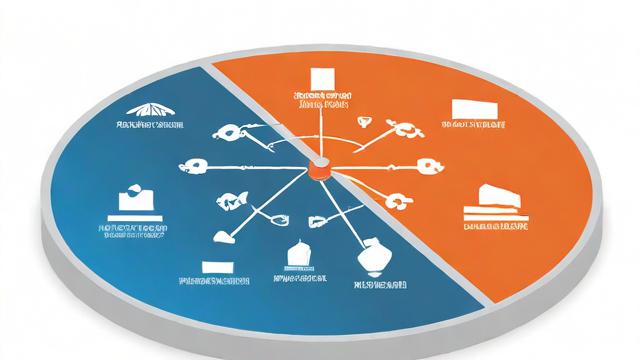
问题2:如何通过5S管理提高员工的安全意识?
回答:通过5S管理提高员工的安全意识可以从以下几个方面入手:一是在整理环节,让员工参与清理工作场所,使他们认识到杂乱的环境对安全的危害;二是在整顿环节,明确各区域的用途和物品的放置规定,同时加强安全标识的设置,让员工在日常工作中不断强化安全意识;三是在清扫环节,鼓励员工发现和报告潜在的安全隐患;四是在清洁环节,制定严格的清洁标准和流程,让员工养成良好的卫生习惯和安全意识;五是在素养环节,加强对员工的安全培训和教育,培养他们的自律意识和责任感。
小编有话说
5S管理不仅仅是一种现场管理方法,更是一种安全管理理念,它通过整理、整顿、清扫、清洁和素养这五个环节的相互配合和协同作用,从多个方面保障了工作场所的安全,虽然5S管理中没有明确单独提出“安全”,但只要将5S管理做到位,就能有效地预防安全事故的发生,为企业创造一个安全、高效、有序的工作环境,企业在推行5S管理时,应注重每个环节与安全的结合,充分发挥5S管理的安全价值。