6s中八大浪费是:过量生产、等待时间、运输、库存、工序不良、动作停顿、缺陷和忽视创造力。
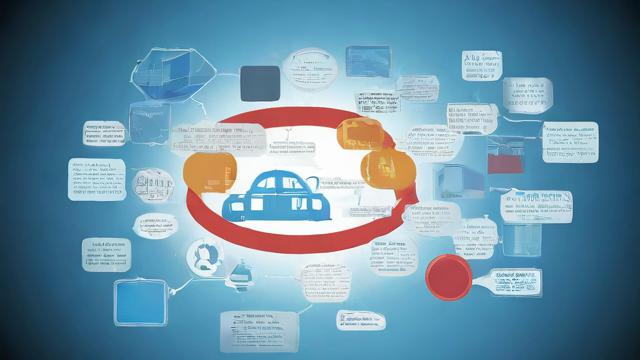
在精益生产理论中,“6S”通常指的是整理(SeiRi)、整顿(Seiton)、清扫(Seiso)、清洁(Seiketsu)、素养(Shitsuke)和安全(Security),而“八大浪费”则是由丰田生产方式提出的概念,包括:过量生产的浪费、等待的浪费、运输的浪费、加工的浪费、库存的浪费、动作的浪费、不良品的浪费以及潜能未被利用的浪费,以下是对这八大浪费的详细解释:
浪费类型 | 描述 | 示例 |
过量生产的浪费 | 生产超过需求的产品,导致库存积压和资源浪费 | 生产了比订单更多的产品,造成仓库空间占用 |
等待的浪费 | 人员或设备等待任务分配或前一工序完成 | 机器闲置等待原材料,员工等待工作指派 |
运输的浪费 | 不必要的物料搬运和移动 | 长距离搬运原材料,频繁转移半成品 |
加工的浪费 | 超出质量标准要求的加工和操作 | 过度精细加工,多余的工序 |
库存的浪费 | 过多的原材料、在制品和成品库存 | 大量原材料积压,过多的成品库存 |
动作的浪费 | 无效或不必要的动作和流程 | 频繁弯腰、转身等不必要的动作 |
不良品的浪费 | 生产过程中产生的不合格品和返工 | 产品缺陷导致报废或需要重工 |
潜能未被利用的浪费 | 员工的创造力和潜力没有得到充分发挥 | 员工有好的改进意见但未被采纳 |
相关问答FAQs
Q1: 如何减少等待的浪费?
A1: 减少等待的浪费可以通过优化生产计划和调度来实现,确保人员和设备的高效利用,通过实施拉动生产系统(如看板管理),只在有需求时才生产,可以显著减少等待时间,提高自动化水平和灵活性,使生产线能够快速适应不同的生产需求,也是减少等待浪费的有效方法。
Q2: 为什么动作的浪费被认为是一种浪费?
A2: 动作的浪费被认为是一种浪费,因为它消耗了时间和能量,却没有增加任何价值,不必要的动作会导致生产效率降低,员工疲劳,甚至可能引发工伤,通过重新设计工作流程和工作站布局,消除不必要的动作,可以提高工作效率,减轻员工负担,从而提高整体生产力。
小编有话说
在日常的生产和管理活动中,识别并消除这些浪费是提升效率、降低成本的关键,企业应该持续关注这些浪费点,不断寻求改进的机会,通过实施精益生产和持续改进的原则,企业不仅能够提高生产效率,还能增强竞争力,实现可持续发展,培养员工的节约意识和参与意识,让每个人都成为改善的一部分,是实现这一目标的重要途径,细节决定成败,小小的改变往往能带来巨大的效益。