精益生产第一阶段是识别浪费,分析价值流,消除不增值活动。
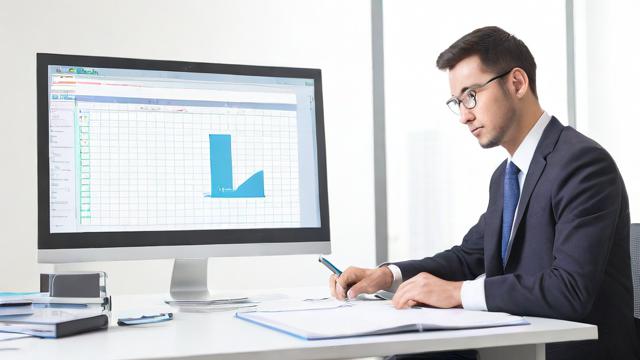
奠定坚实基础的关键时期
在当今竞争激烈的商业环境中,企业为了提高效率、降低成本、提升质量,纷纷引入精益生产方式,精益生产的实施并非一蹴而就,而是一个循序渐进的过程,其中第一阶段作为整个精益之旅的起始点,具有至关重要的意义,这一阶段主要聚焦于理念导入与现状评估,为企业后续的精益变革筑牢根基。
理念导入:播下精益思想的种子
精益生产源于丰田生产系统,其核心思想是以客户需求为导向,通过消除浪费、优化流程和持续改进,实现企业的高效运营,在第一阶段,企业的首要任务是将精益理念全方位地导入组织内部,确保从高层管理人员到一线员工都能深入理解并认同这些理念。
这通常通过开展一系列培训活动来实现,邀请精益专家进行内部培训课程,详细讲解精益生产的起源、发展、基本原则(如消除七大浪费:过量生产、等待时间、运输、过度加工、库存积压、不必要的动作、不良品)以及常见的精益工具(如 5S 现场管理法、价值流分析等),组织员工观看相关的精益生产纪录片或案例视频,让他们直观地感受精益理念在其他企业成功应用所带来的巨大效益,从而激发员工对精益生产的兴趣和积极性。
除了培训,高层领导的支持与参与也不可或缺,他们需要在企业内部会议上强调精益生产的重要性,将其纳入企业的战略规划,并亲自参与到一些精益项目的启动活动中,为全体员工树立榜样,营造积极的精益文化氛围。
现状评估:绘制企业运营的真实蓝图
在员工对精益理念有了初步认识之后,企业需要对自身的运营现状进行全面而细致的评估,这一过程就像是给企业进行一次全面的“体检”,旨在找出存在的问题、瓶颈以及潜在的改进机会,为后续制定针对性的精益改进策略提供依据。
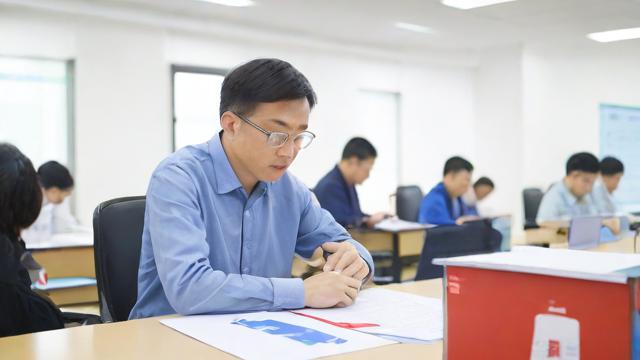
现状评估涵盖了多个方面,包括但不限于生产流程、供应链管理、质量管理、设备维护以及人员配置等,在生产流程方面,通过绘制价值流图,详细分析从原材料采购到产品交付给客户的整个过程中哪些是增值活动,哪些是非增值活动,从而发现流程中的等待时间过长、物料搬运不合理等问题,在质量管理方面,收集产品质量数据,分析缺陷类型及其产生的原因,评估质量控制体系的有效性。
为了确保评估结果的准确性和客观性,企业可以采用多种数据收集方法,如实地观察、员工访谈、问卷调查以及数据分析等,借助一些专业的评估工具,如精益成熟度模型(LMM),对企业的精益水平进行量化评估,明确企业在精益道路上所处的位置以及与标杆企业之间的差距。
以下是一个简单的现状评估表格示例:
评估维度 | 发现问题 | |
生产流程 | 生产节拍、工序安排 | 生产线平衡率较低,部分工序等待时间长 |
供应链管理 | 供应商交货准时率、库存周转率 | 供应商交货不稳定,库存积压严重 |
质量管理 | 产品合格率、质量投诉处理 | 质量问题频发,质量追溯困难 |
设备维护 | 设备故障率、维护保养计划执行 | 设备老化,预防性维护不足 |
人员配置 | 员工技能水平、工作负荷 | 员工技能单一,部分岗位工作负荷不均 |
相关问答 FAQs
问题 1:精益生产第一阶段的理念导入培训应该持续多久?
答:理念导入培训的持续时间因企业规模、员工素质以及培训内容的深度而异,对于小型企业可能只需要几天到几周的时间进行集中培训;而对于大型企业,可能需要数月甚至半年以上的时间来分阶段、分层次地推进培训,以确保所有员工都能充分理解和吸收精益理念,重要的是培训不能仅仅停留在理论层面,还需要通过实际案例分析和模拟演练等方式让员工能够将所学知识应用到工作中。
问题 2:现状评估过程中,如果不同部门对评估结果存在分歧该怎么办?
答:在现状评估中出现部门间分歧是比较常见的情况,应鼓励各部门充分表达自己的观点和理由,促进沟通与交流,由跨部门的团队对分歧点进行深入分析,从整体业务流程和企业战略的高度来审视问题,如果仍然无法达成一致,可以考虑引入外部专家或顾问进行中立的评判和协调,确保评估结果能够真实反映企业的实际情况,为后续的精益改进提供可靠的依据。
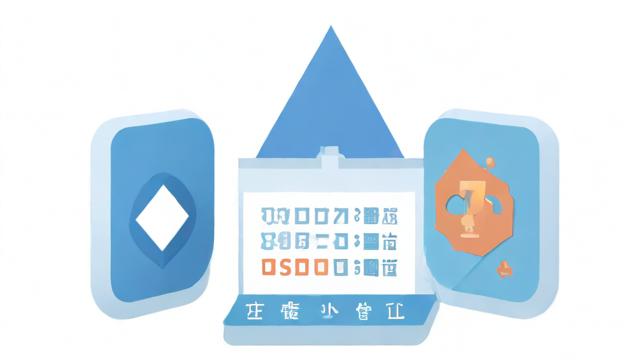
小编有话说
精益生产第一阶段虽然只是整个精益变革的开端,但它如同建造高楼大厦时打下的坚实地基,决定着后续楼层能否稳固矗立,企业在这一阶段投入的时间和精力都将为后续的流程优化、成本降低和质量提升奠定坚实的基础,只有扎实做好理念导入和现状评估工作,才能在精益生产的道路上稳步前行,逐步实现企业的卓越运营和可持续发展。