6S安全实施方法指的是通过整理、整顿、清扫、清洁、素养、安全这六个步骤,来优化工作环境和提升安全管理水平的方法。
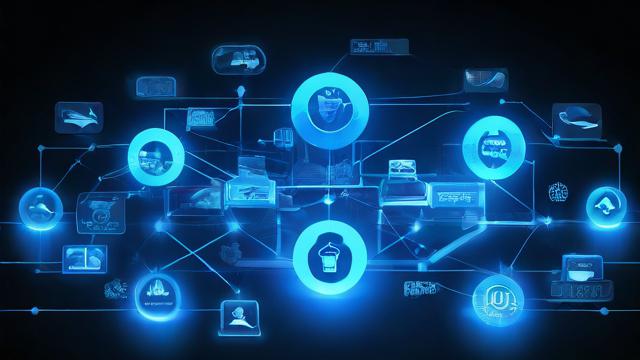
6S 安全实施方法详解
一、6S 概述
6S 管理源于日本的 5S 管理,在整理(Seiri)、整顿(Seiton)、清扫(Seiso)、清洁(Seiketsu)的基础上增加了安全(Safety)要素,旨在通过规范现场、现物,营造一目了然的工作环境,培养员工良好的工作习惯,最终提升企业的安全管理水平与工作效率,前 4S 是基础,安全则是核心保障,确保整个工作场景处于可控、无隐患状态,预防事故发生,保障人员健康与生产顺利进行。
二、各 S 在安全实施中的内涵
(一)整理(Seiri)
含义:区分工作现场的必需品和非必需品,将非必需品移除工作区域,在安全层面,非必需物品随意堆放可能绊倒人员、阻塞逃生通道,或是造成物料误混引发危险反应,例如在化工车间,多余的化学试剂包装若不清理,堆积在过道,工人搬运大型设备时就可能被绊倒;在机械加工车间,废弃的金属边角料若散落一地,容易被叉车碾压弹起伤到周边操作人员。
安全实施要点:定期盘点工位、仓库等区域物品,制定清晰的必需品判定标准,依据工作流程确定每件物品留存必要性;设立专门的废弃物回收区,并安排定时清理,确保无杂物堆积;对新入职员工培训整理原则,使其能自主判断与维护现场整洁有序,减少安全隐患滋生土壤。
(二)整顿(Seiton)
含义:把必需品依规定位置、方法摆放,并明确标识,方便取用与归位,从安全视角出发,物品乱摆乱放会延长寻找时间,增加操作失误风险,紧急情况下还阻碍应急响应,像消防器材若未固定位置、无醒目标识,火灾发生时难以迅速找到使用;危险化学品若存放混乱,拿错试剂可能引发剧烈化学反应致灾。
安全实施要点:规划合理存储空间,为各类工具、物料划分专属区域,如工具采用形迹管理,挂于对应模具上;制作清晰、准确、耐用的标识牌,包含品名、规格、有效期、操作注意事项等关键信息,张贴于显眼处;建立物品领用登记制度,实时掌握物品流向,防止因无序取用导致安全失控。
(三)清扫(Seiso)
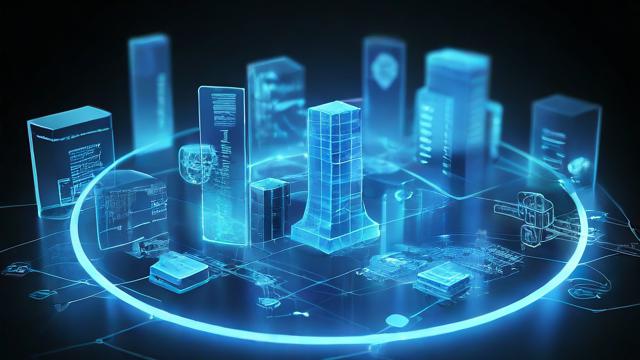
含义:清除工作场所内的脏污,防止污染、故障发生,维持设备与环境良好状态,脏污不仅影响美观,更藏纳安全隐患,油污地面易使人滑倒摔伤;设备积尘过多可能引发散热不良、短路等问题,威胁设备运行安全与人员操作安全。
安全实施要点:制定日常清扫计划,明确责任区域与清扫频次,如每日下班前 15 分钟全员参与工位周边清扫;针对重点部位(如设备关键部件、高温高压管道接口)加大清扫力度,采用专业清洁工具与清洁剂;建立检查机制,主管定期巡查清扫效果,发现问题及时整改,将清扫融入日常工作规范,杜绝灰尘污垢积累成患。
(四)清洁(Seiketsu)
含义:将整理、整顿、清扫的做法制度化、规范化,维持前 3S 成果,形成长效保持机制,没有清洁环节固化流程,前期努力易反弹,安全隐患死灰复燃,例如刚整理整顿好的车间,若缺乏持续监督,员工很快又随意摆放物品、恢复脏乱。
安全实施要点:成立专门 6S 推行小组,负责制定标准化作业文件,涵盖各环节操作流程、检查标准、奖惩措施;定期开展 6S 培训与考核,强化员工执行意识,使规范成为习惯;建立监督检查体系,管理层不定期抽查,依据结果奖优罚劣,推动 6S 理念深入企业文化,保障安全环境持久稳定。
(五)安全(Safety)
含义:消除一切不安全因素,构建安全工作环境,这是 6S 核心目标,贯穿全程,涉及人的操作安全、设备运行安全、物料存储安全及环境条件安全等多维度,如电气设备未接地、防护装置缺失,人员违规操作等都是典型安全隐患。
安全实施要点:开展全面安全检查,定期(日检、周检、月检)排查设备设施、作业流程、人员行为隐患;建立隐患台账,对发现的问题分级分类,明确整改责任人与期限,跟踪整改落实;加强员工安全培训,包括三级安全教育、特种作业培训、事故案例警示,提升全员安全素养;完善应急预案,定期演练,确保突发状况下人员能迅速、有序应对,降低损失。
三、6S 安全实施步骤
阶段 | 主要任务 | |
启动阶段 | 组建团队、宣传动员 | 选拔涵盖各层级人员的 6S 推行小组;召开启动大会,讲解 6S 知识、意义与目标,利用海报、标语、内部刊物营造氛围 |
规划阶段 | 制定方案、设定标准 | 结合企业实际,细化 6S 各环节实施细节;明确各区域、岗位 6S 执行标准,如车间工具摆放标准、仓库货物堆码规范;制定奖惩制度激励员工参与 |
实施阶段 | 全员行动、逐步推进 | 按规划方案分区域、分阶段开展整理、整顿等工作;现场指导员工操作,及时纠正不规范行为;定期归纳经验,调整优化实施策略 |
检查阶段 | 自查自纠、上级验收 | 员工每日对照标准自查;部门间交叉互查;管理层定期巡检;依据检查结果评分排名,表彰优秀、督促后进 |
巩固阶段 | 持续改进、文化植入 | 分析检查问题根源,修订制度标准;将 6S 成果融入企业日常运营,新员工入职即接受 6S 培训;定期回顾归纳,不断拓展 6S 深度广度 |
四、6S 安全实施效益
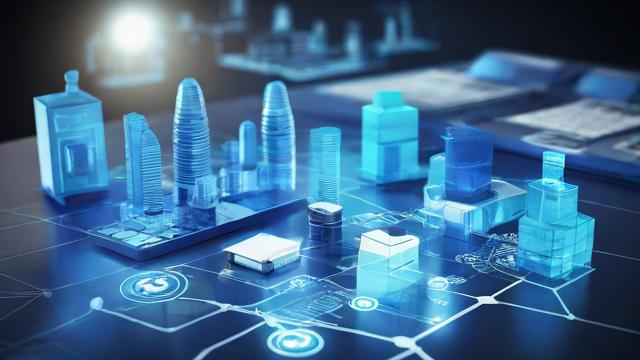
事故预防:通过消除隐患、规范行为,大幅降低工伤、火灾、爆炸等事故发生概率,保障员工生命健康与企业财产安全。
效率提升:物品定位便捷取用、环境整洁有序,缩短作业准备与寻找时间,设备稳定运行减少故障停机,整体提高生产效率。
成本降低:减少因事故导致的医疗赔偿、设备维修、生产延误等直接成本;优化空间利用、精准物料管控节约库存与资源浪费成本。
形象改善:整洁规范的企业面貌提升客户信赖度、员工归属感,利于市场开拓与企业长远发展。
五、相关问答 FAQs
Q1:6S 实施过程中员工积极性不高怎么办?
A1:首先了解员工抵触原因,可能是培训不足、未看到实效或奖惩不明,针对性强化培训,展示成功案例;优化奖励机制,让员工切实受益;设立意见箱,鼓励员工提建议参与改进,增强其主人翁意识。
Q2:中小企业资源有限如何有效推行 6S?
A2:可先选取关键区域试点推行,聚焦核心问题突破;利用内部骨干力量带动全员;简化定制一些低成本标识工具;灵活运用手机拍照对比等方式监督整改;借鉴同行经验少走弯路,循序渐进扩大推行范围。
小编有话说
6S 安全实施绝非一朝一夕之功,它是一场全员参与、持续改进的企业变革,企业需秉持坚定决心,从细微处入手,将 6S 理念深植每位员工心中,以严谨态度落实每个环节,唯有如此,才能筑牢安全防线,在高效、有序运营轨道上稳健前行,收获长期经济效益与社会效益双丰收,实现可持续发展愿景,让 6S 成为企业成长的坚实助力而非流于形式的口号。