**5S中的七大浪费通常指的是:**,,1. **过量生产的浪费**,2. **等待的浪费**,3. **运输的浪费**,4. **过度加工的浪费**,5. **库存的浪费**,6. **动作的浪费**,7. **不良品的浪费**
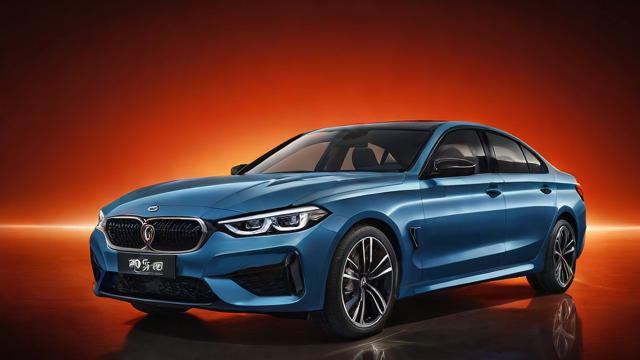
在精益生产理论中,“5S”是一套用于组织、清洁和维护工作场所的方法和原则,其目的是创建一个更高效、更安全的工作环境,而“七大浪费”(Seven Wastes),又称为“丰田生产系统的七种浪费”,则是识别和消除生产过程中不增值活动的工具,下面将详细解释这七大浪费:
序号 | 浪费类型 | 描述 | 示例 |
1 | 过量生产 | 生产超过需求的产品,导致库存积压和资源浪费 | 生产了比客户需求更多的产品,造成仓库空间占用和资金占用 |
2 | 等待 | 人员或机器闲置,等待下一步操作或物料供应 | 生产线上工人等待物料送达,或者设备故障导致的停工等待维修 |
3 | 运输 | 不必要的物料搬运或人员移动 | 频繁地将半成品从一个工作站转移到另一个工作站,增加了搬运时间和成本 |
4 | 过度加工 | 进行超出客户要求的加工或检验 | 对产品进行多余的加工步骤,比如过于严格的质量检测,增加了生产成本 |
5 | 库存 | 存储过多的原材料、在制品或成品 | 大量库存占用资金和空间,可能掩盖生产问题,如质量问题或延迟交货 |
6 | 运动/动作 | 人员在工作中做出的无效或低效的动作 | 员工在工作中频繁弯腰、转身等不必要的动作,消耗体力且降低效率 |
7 | 缺陷产品 | 生产出不符合标准的产品,需要返工或报废 | 产品出现缺陷,需要重新加工或直接报废,造成材料和人力资源浪费 |
相关问答FAQs
Q1: 如何区分“5S”与“七大浪费”?
A1: “5S”主要关注于工作场所的组织和管理,包括整理(Seiri)、整顿(Seiton)、清扫(Seiso)、清洁(Seiketsu)和素养(Shitsuke),旨在创造一个有序、高效的工作环境,而“七大浪费”则侧重于识别和消除生产过程中的不增值活动,两者虽然目的相似,但侧重点不同。
Q2: 实施“5S”和减少“七大浪费”对企业有什么好处?
A2: 实施“5S”可以提高工作效率,减少寻找工具和材料的时间,提升员工的工作满意度和安全性,减少“七大浪费”则可以直接降低生产成本,提高产品质量,缩短交货时间,增强企业的市场竞争力,两者结合使用,可以显著提升企业的整体运营效率和盈利能力。
小编有话说
在当今竞争激烈的市场环境中,企业要想保持竞争力,就必须不断优化内部流程,提高效率,通过实施“5S”管理方法和识别并减少“七大浪费”,企业不仅可以降低成本,还能提升员工的工作效率和满意度,这些方法看似简单,但长期坚持下来,将为企业带来巨大的改变,希望每个企业都能重视起来,从细节做起,逐步实现精益生产,走向成功。