丰田TPS的七大浪费包括过量生产、等待时间、运输、过度加工、库存、运动和缺陷。
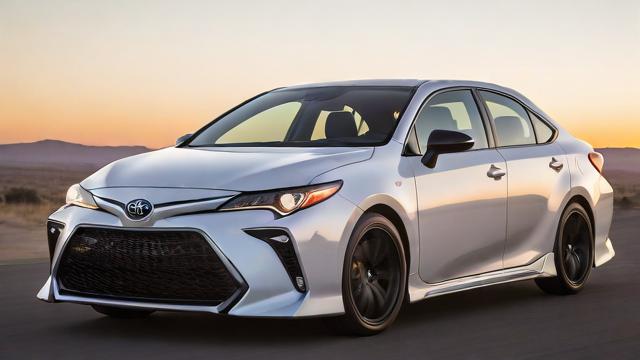
丰田TPS(Toyota Production System,即丰田生产方式)的七大浪费是生产管理中需要识别和消除的关键浪费类型,它们阻碍了生产效率的提升和成本的降低,以下是这七大浪费的详细解释:
浪费类型 | 描述 |
生产过剩 | 生产过剩指的是生产出超过需求的产品,这是最严重的一种浪费,它不仅占用了过多的资源,还可能导致库存积压、资金占用和产品过时等问题,生产过剩往往源于对市场需求预测不准确、生产计划不合理或过度追求生产效率而忽视实际需求。 |
等待 | 等待是指在生产过程中,由于设备故障、材料短缺、生产计划不协调等原因导致的人员或设备闲置,这种浪费直接影响了生产效率,增加了生产成本,并可能延误交货期。 |
运输 | 运输浪费包括不必要的物料搬运和移动,在生产过程中,原材料、半成品和成品的过度搬运不仅增加了时间成本,还可能因搬运不当导致产品损坏或质量下降,优化生产布局和物流流程是减少运输浪费的关键。 |
不适当的处理过程 | 不适当的处理过程指在生产过程中使用了不必要的复杂工艺、设备或操作步骤,这些过度加工的活动不仅增加了生产成本,还可能降低产品质量和生产效率,简化工艺流程、采用更高效的生产方法是减少这种浪费的有效手段。 |
不必要的存货 | 不必要的存货是指过量的原材料、半成品和成品库存,库存占用了大量资金和空间,同时可能掩盖生产过程中的问题,实施准时化生产(JIT)、优化库存管理和减少安全库存量是降低库存浪费的重要措施。 |
不必要的动作 | 不必要的动作包括员工在生产过程中进行的多余或无效的动作,如过度走动、重复动作等,这些动作不仅消耗了员工的体力和时间,还降低了生产效率,通过工作分析和流程改进,可以消除不必要的动作浪费。 |
过失 | 过失浪费指的是由于生产缺陷或质量问题导致的返工、报废等额外成本,这种浪费不仅增加了生产成本,还可能影响企业的声誉和客户满意度,加强质量控制、提高员工技能水平和引入质量管理体系是减少过失浪费的关键。 |
丰田TPS的七大浪费涵盖了生产管理的各个方面,识别并消除这些浪费对于提升企业竞争力具有重要意义。