精益管理八步法通常被称为**精益八步法**,它包括明确目标、现状分析、确定改进点、制定改进计划、实施改进、持续监控、评估效果和持续改进。
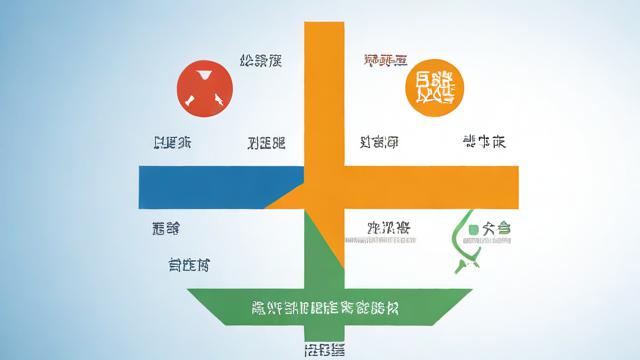
精益管理八步法详解
精益管理是一种旨在消除浪费、优化流程、提高效率和质量的管理理念与方法体系,在企业运营和发展中发挥着重要作用,精益管理八步法是一套系统且实用的实施步骤,以下是其详细介绍:
第一步:明确价值
这是精益管理的起点,也是核心基础,所谓“价值”,是指从顾客角度出发,顾客愿意付费购买的产品或服务所具备的功能和特性,即满足顾客明确需求的东西,对于一家汽车制造企业,顾客购买汽车可能是为了日常出行的便利性、安全性以及一定的舒适性和品牌形象等,这些都是价值所在,企业需要通过市场调研、客户反馈收集、订单分析等方式,精准地确定顾客真正需要什么,哪些是顾客认为有价值的产品特性和服务内容,避免生产或提供顾客不需要或不认可的产品与服务,从而避免资源浪费在非价值创造活动上。
方法 | 说明 | 示例 |
市场调研 | 了解目标市场趋势、顾客偏好变化等信息 | 调查消费者对汽车颜色、内饰风格的喜好 |
客户反馈收集 | 通过售后回访、在线评价等渠道获取意见 | 收集车主对车辆操控性能、油耗方面的反馈 |
订单分析 | 研究顾客订单中的详细需求规格 | 分析企业订单中不同配置车型的比例和需求特点 |
第二步:识别价值流
在明确价值之后,就要找出从原材料到交付成品给顾客的整个生产过程中哪些是增值的活动,哪些是非增值但却消耗资源的活动,也就是价值流,增值的活动通常包括直接加工产品使其符合质量标准、按照顾客要求进行组装等;而非增值活动可能涵盖过量库存积压、不必要的搬运和等待时间等,在电子产品制造中,直接将合格电子元件焊接到电路板上使其形成完整电路模块是增值活动,但原材料因库存管理不善导致的长时间堆积在仓库未使用则是明显的浪费,属于非增值活动,识别价值流需要对整个生产流程进行详细的梳理和分析,绘制价值流图,清晰展示每个环节的价值创造和浪费情况,以便后续采取措施消除浪费。
类型 | 示例 |
增值活动 | 机械加工零件使其达到精确尺寸 |
非增值活动 | 原材料过量库存导致资金占用和仓储空间浪费 |
第三步:让价值流动起来
当识别出价值流后,关键就是要采取措施消除浪费,使价值能够顺畅地在企业内部各个环节流动,减少中断和等待时间,这可能需要对企业的布局进行重新规划,优化物流配送路线,建立高效的信息沟通机制等,一家服装制造企业可以采用看板管理系统来拉动生产,根据销售终端的实际销售情况及时调整生产和物料配送计划,确保布料、纽扣等原材料在需要的时候恰好到达相应的生产工序,而不是过早或过晚,从而实现价值的快速流动,提高生产效率和响应市场的速度。
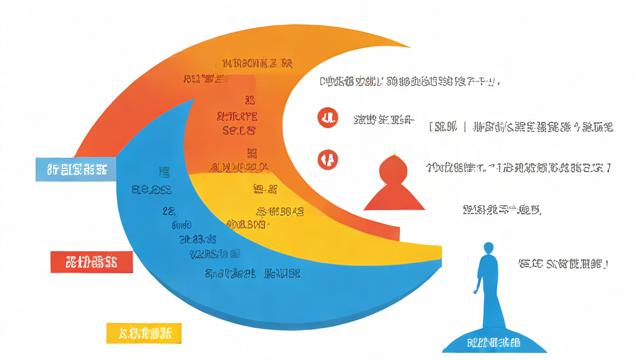
第四步:拉式生产
拉式生产是一种与传统推式生产截然不同的生产组织方式,在推式生产中,生产过程往往是根据生产计划部门制定的生产计划,从原材料采购开始,依次推动各个生产环节进行加工,最终将产品推向市场,这种方式容易导致库存积压和生产与市场需求脱节的问题,而拉式生产则是以顾客的需求为起点,由后工序向前工序提出需求,前工序根据需求进行生产和供应,在家具制造中,销售部门接到顾客订单后,将订单信息传递给组装车间,组装车间根据所需家具的款式和数量向木工车间提出木材加工的具体要求,木工车间再按照要求进行木材切割、打磨等加工,这样就能精准地控制生产数量和进度,有效降低库存水平,提高生产的灵活性和适应性。
第五步:追求尽善尽美
精益管理是一个持续改进的过程,追求尽善尽美意味着企业不能满足于现有的成果和状态,要不断地寻找进一步优化的机会,这涉及到对产品质量、生产效率、成本控制等各个方面的持续关注和提升,企业可以通过开展质量小组活动,鼓励员工提出改进建议和创新想法;定期对生产流程进行审计和评估,发现潜在的问题和不足之处;引入先进的技术和管理方法,如自动化设备升级、信息化管理系统的应用等,不断推动企业向更高的管理水平迈进,一家制药企业在药品生产过程中,持续优化生产工艺参数,提高药品的纯度和稳定性,同时加强员工培训,提升操作技能和质量意识,以追求产品质量的极致完美,增强企业在市场中的竞争力。
第六步:全员参与
精益管理的成功离不开全体员工的积极参与和支持,企业要从高层管理者到一线员工,都树立精益的理念和意识,明确自己在精益改进过程中的角色和责任,高层管理者需要制定明确的精益战略和目标,为精益管理的推行提供资源保障和政策支持;中层管理人员要负责组织实施具体的精益项目和活动,协调各部门之间的工作;基层员工则要积极参与到价值流分析、问题解决等实际操作中,发挥自身的智慧和创造力,通过开展精益培训课程、设立员工奖励制度等方式,激励员工主动参与到精益管理活动中来,形成良好的精益文化氛围。
第七步:建立精益文化
建立精益文化是精益管理深入企业骨髓的关键,精益文化强调持续改进、消除浪费、追求卓越的价值观,使这些理念成为企业全体员工共同的行为准则和思维方式,在这种文化氛围下,员工会自觉地关注工作流程中的浪费现象,积极主动地寻求改进机会,并且相互协作、相互学习,共同推动企业的发展,企业可以通过内部宣传栏、企业文化活动、案例分享会等多种渠道传播精益文化,让新员工入职时就能感受到这种浓厚的文化气息,老员工则不断强化和传承精益理念,使精益文化在企业内部生根发芽、开花结果。
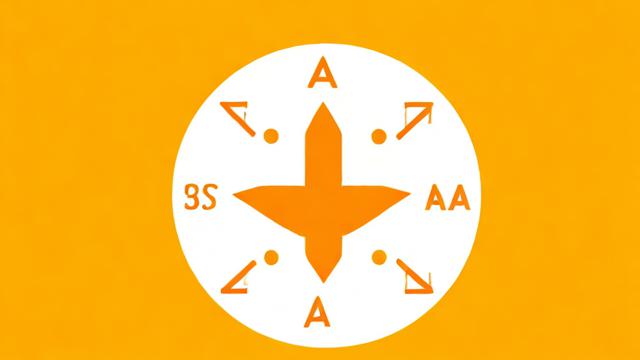
第八步:持续改进
精益管理的最后一个步骤是持续改进,这也是贯穿整个精益管理过程的永恒主题,企业要根据市场环境的变化、顾客需求的演变以及内部生产过程中出现的新问题和新挑战,不断地调整和完善精益管理的方法和措施,持续改进需要一个系统的循环机制,包括设定改进目标、收集数据、分析问题、制定改进方案、实施改进措施以及评估改进效果等环节,周而复始,不断推动企业向更高水平发展,随着环保要求的日益严格,一家化工企业需要持续改进其生产工艺,减少污染物排放,同时提高能源利用效率,这就需要企业持续关注相关政策法规变化和技术发展趋势,不断探索新的改进途径和方法。
FAQs
问题一:精益管理八步法是否适用于所有行业?
答案:精益管理八步法具有广泛的适用性,虽然它起源于制造业,如丰田生产方式,但在众多其他行业也同样有效,无论是服务业(如银行、医院、酒店)、物流行业、信息技术行业还是公共部门(如政府部门的一些行政服务流程),都可以根据自身的特点和需求应用精益管理八步法,银行可以通过明确顾客办理业务时的价值需求(如快速准确的金融服务),识别业务流程中的价值流(如贷款审批流程中的繁琐手续),然后采取措施让价值流动起来(如简化审批流程、优化线上服务平台),以实现提高服务效率、降低成本、提升顾客满意度的目标,只要企业或组织存在流程优化和价值创造的需求,精益管理八步法都能提供有益的指导框架。
问题二:实施精益管理八步法需要多长时间才能看到明显成效?
答案:实施精益管理八步法看到明显成效的时间因企业的情况而异,没有一个固定的时间表,这取决于多个因素,如企业的规模大小、行业特点、现有流程的复杂程度、员工对精益理念的接受程度以及企业投入的资源多少等,一些小型企业在简单业务流程上的初步改进可能在几个月内就能看到一定的成效,比如库存周转率提高、部分生产环节的浪费减少等,但对于大型企业或复杂的生产系统,可能需要一年甚至更长时间才能在整体绩效上有显著的提升,重要的是企业要保持耐心和持续的努力,不能因为短期内看不到明显效果就半途而废,要将精益管理作为一个长期的战略规划持续推进,逐步积累改进成果,实现企业的持续发展和竞争力提升。
小编有话说:精益管理八步法为企业提供了一条清晰的通往高效、优质发展的道路,它不仅仅是一套理论方法,更是一种企业管理的变革之旅,企业在实施过程中要结合自身实际情况灵活运用,注重每一个步骤的细节落实和员工的积极参与,这样才能逐步构建起强大的精益管理体系,在激烈的市场竞争中脱颖而出,实现可持续发展的长远目标。