6S管理第一步是整理(SEIRI),区分必需品与非必需品,清理工作现场。
一、6S管理概述
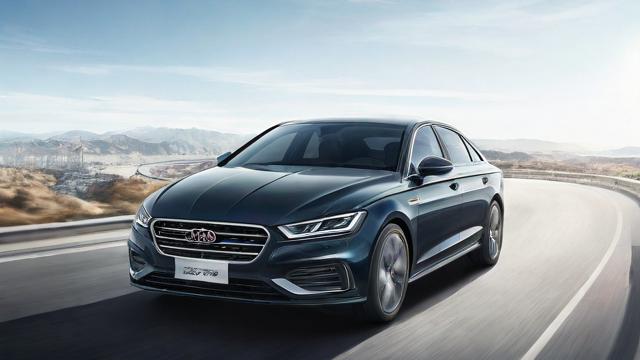
6S管理源于日本的5S管理,在整理(SEIRI)、整顿(SEITON)、清扫(SEISO)、清洁(SEIKETSU)、素养(SHITSUKE)的基础上增加了安全(SAFETY),因其英文单词均以“S”开头,简称6S,6S管理是一种旨在提升企业现场管理水平、提高工作效率、保障产品质量和员工安全的综合性管理方法,广泛应用于制造业、服务业等众多领域。
二、6S第一步 - 整理(SEIRI)
1、定义与目的
- 整理是将工作场所的任何物品区分为有必要和没有必要的,除了有必要的留下来,其他的都消除掉,其目的在于腾出空间,空间活用,防止误用,塑造清爽的工作场所,在一个生产车间里,将长期闲置不用的设备、多余的原材料、废弃的工具等清理出去,使车间的空间得到释放,工作人员能够更高效地开展工作。
2、实施步骤
全面检查:对工作场所进行全面细致的检查,包括设备、工具、原材料、文件、办公用品等所有物品,可以制定详细的检查表,按照区域或类别逐一进行记录。
区分必需品和非必需品:根据物品的使用频率、重要性等因素判断其是否为必需品,正在生产中使用的生产设备、每天需要查看的文件等为必需品;而损坏且无法修复的设备、过时的文件等则为非必需品。
清理非必需品:对于非必需品,可以采取不同的处理方式,如仍有使用价值的物品,可以考虑转赠、变卖等;对于无价值的物品,如废弃的纸张、塑料等,则直接丢弃。
3、注意事项
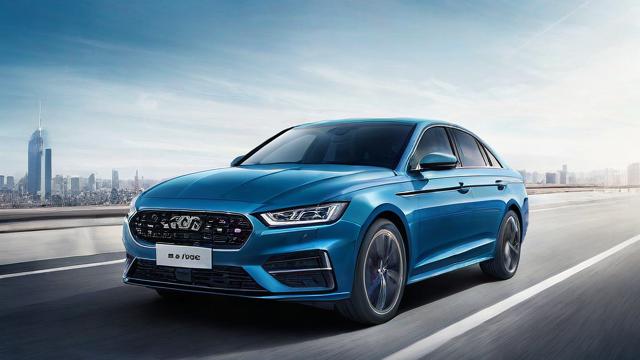
- 在区分必需品和非必需品时,要充分考虑实际工作需求和工作流程,避免因过度清理而影响正常工作,整理工作不是一次性的,需要定期进行复查和持续改进,以确保工作场所始终保持整洁有序。
三、整理的意义与作用
1、提高工作效率:通过清理不必要的物品,减少了寻找工具、材料和文件的时间,员工能够更快地进入工作状态,从而提高整体工作效率。
2、保障安全生产:过多的杂物堆积可能会造成通道堵塞、绊倒等安全隐患,整理后,工作场所更加宽敞,通道畅通,降低了事故发生的可能性。
3、提升企业形象:一个整洁、有序的工作场所会给来访客户、合作伙伴留下良好的印象,有助于提升企业的外部形象和市场竞争力。
四、相关案例
某制造企业在实施6S管理之前,车间内各种物品随意摆放,过道被占用,导致生产效率低下,安全事故频发,在推行整理阶段,企业成立了专门的6S小组,对车间进行了全面的检查和清理,经过一个月的努力,共清理出闲置设备10台、废旧材料5吨、过期文件200份等,车间空间得到了有效利用,生产效率提高了20%,安全事故发生率明显降低。
五、FAQs
问题1:在整理过程中,如何确定某些不常用的物品是否为必需品?
答:对于不常用的物品,可以从以下几个方面考虑其是否为必需品,考虑物品的使用周期,如果该物品虽然不常用,但每隔一段时间就必须要使用一次,且对生产或工作有重要影响,那么它可以被视为必需品,分析物品的潜在价值,例如某些备用设备,虽然平时不使用,但在设备故障或紧急情况下能够发挥关键作用,也应保留,结合行业标准和法规要求,有些物品可能是为了满足特定的合规性而必须配备的,即使使用频率低,也不能随意清理。
问题2:整理工作完成后,如何保持工作场所的长期整洁?
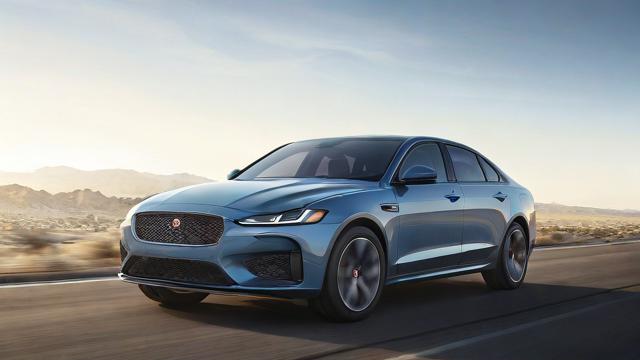
答:要保持工作场所的长期整洁,需要建立一系列的制度和措施,一是制定明确的清洁责任区域和责任人,确保每个区域都有专人负责日常清洁和维护;二是建立定期巡查机制,由专人定期检查工作场所的整理情况,及时发现并纠正不符合要求的地方;三是加强员工培训和教育,提高员工对6S管理的认识和理解,培养他们自觉遵守整理规定的习惯;四是持续优化工作流程和布局,从源头上减少不必要的物品产生和堆积。
小编有话说
6S管理中的整理作为第一步,是整个管理体系的基础和关键环节,它不仅能够帮助企业改善工作环境,提高工作效率和安全性,还能为企业带来诸多潜在的效益,实施整理并非一蹴而就,需要企业全体员工的共同参与和持续努力,在实际工作中,企业应根据自身的特点和需求,灵活运用6S管理的方法和技巧,不断探索适合自身的管理模式,以实现企业的可持续发展,希望以上内容能对大家理解和实施6S管理中的整理环节有所帮助。