瀚宇博德压合课主要负责半导体封装中芯片的压合工序,确保芯片与基板等有效结合。
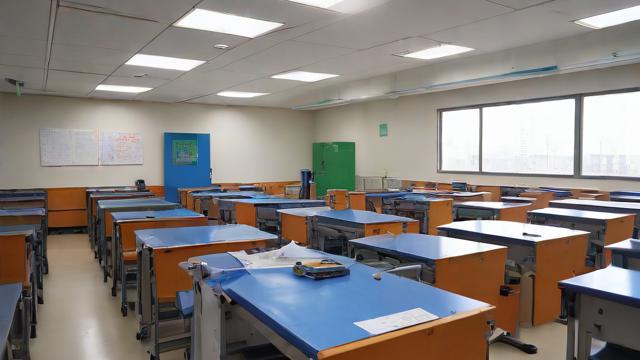
详解
在瀚宇博德的生产过程中,压合课扮演着极为关键的角色,其主要工作涵盖了从前期准备到压合操作以及后续的质量管控等多个环节,以下是其详细的工作内容介绍:
一、前期准备工作
(一)物料准备
1、芯板准备
- 根据生产计划单,从原材料仓库领取相应规格和型号的芯板,在领取过程中,需仔细核对芯板的材质、厚度、尺寸等参数,确保与生产要求完全一致,对于某一款高端多层电路板的生产,其芯板可能采用特殊的高性能树脂材料,厚度公差要求控制在±0.05mm 以内,压合课员工需要使用精密的测量工具对芯板进行抽检,保证每一片芯板都符合标准。
- 对领取后的芯板进行外观检查,查看是否有划伤、破损、污渍等缺陷,如有轻微缺陷,需评估是否会影响后续压合及产品质量,若缺陷严重则需及时更换。
2、铜箔准备
- 依据不同的电路设计要求,选择合适的铜箔类型,如电解铜箔或压延铜箔,并确定铜箔的厚度,常见的铜箔厚度有 1/2oz、1oz、2oz 等(1oz ≈ 34μm)。
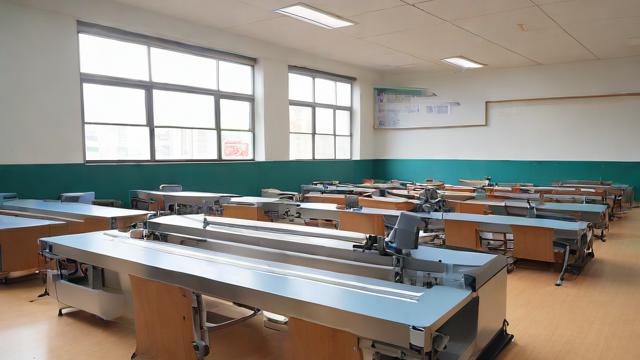
- 检查铜箔的氧化程度,若铜箔表面氧化严重,可能会影响其与芯板之间的粘合力,进而导致压合不良,需要对铜箔进行适当的表面处理,如微蚀、粗化等工艺,以增加其表面的粗糙度和活性,提高结合力。
3、胶片准备
- 根据产品的要求,挑选合适型号的胶片,胶片的种类多样,包括环氧胶片、酚醛胶片等,不同胶片具有不同的粘结性能、耐温性和电气性能,在高频高速电路板的生产中,通常会选用低介电常数、低损耗因数的特种胶片,以满足信号传输的高要求。
- 检查胶片的保质期和储存条件,确保胶片未受潮、未过期且性能良好,按照工艺要求,将胶片裁剪成合适的尺寸,以便与芯板和铜箔进行层压组合。
(二)设备检查与调试
1、压合机检查
- 在启动压合机之前,对设备进行全面的外观检查,查看设备的各部件是否有松动、损坏的迹象,如压合机的加热板是否平整、液压系统是否有泄漏等。
- 检查压合机的温度控制系统、压力控制系统和时间控制系统是否正常工作,通过设定特定的测试温度、压力和时间参数,运行设备进行空载测试,确保实际输出值与设定值相符,误差范围在允许范围内,对于温度控制精度,一般要求在±5℃以内,以确保压合过程中的温度稳定性。
2、辅助设备检查
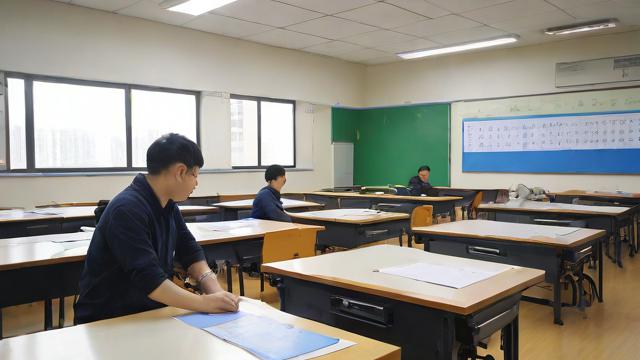
- 检查叠板机、卸板机等辅助设备的运行状况,叠板机应能准确地将芯板、铜箔和胶片按照预定的顺序和位置进行叠放,其叠放精度应控制在±0.1mm 以内;卸板机则要能够平稳地将压合后的板子从压合机中取出,避免对板子造成损伤。
- 对用于清洁和搬运物料的工具进行检查和清洁,如无尘布、吸尘装置、周转车等,确保工具的干净整洁,防止杂质混入生产过程中。
二、压合操作流程
(一)叠板操作
1、内层叠板
- 按照电路设计的层压顺序,先将芯板放置在叠板机的底层,然后在芯板的上下表面分别依次铺设铜箔和胶片,注意铺设过程中要保持材料的平整度,避免出现褶皱或气泡,在制作六层电路板时,从下往上的叠放顺序可能是:芯板 - 铜箔 - 胶片 - 铜箔 - 芯板 - 铜箔 - 胶片。
- 每铺设一层材料,都要使用滚轮或刮板轻轻压实,排除材料之间的空气,使各层材料紧密贴合,对于较厚的板材或多层叠放的情况,可能需要多次重复压实操作,以确保整个叠板结构的稳定性。
2、外层叠板
- 在内层叠板完成后,根据产品的外层线路要求,在最上层和最下层分别铺设外层铜箔和保护膜,保护膜的作用是在压合过程中保护外层铜箔不受损伤,同时也便于后续的加工处理,在一些表面有精细线路的电路板生产中,保护膜可以有效防止铜箔在压合和后续加工过程中被刮擦或氧化。
- 完成所有材料的叠放后,再次对整个叠板进行全面检查,确认材料无错位、无遗漏,并且各层之间的贴合紧密,将叠好的板子平稳地转移到压合机中进行压合操作。
(二)压合工艺参数设置与执行
1、参数设置
- 根据产品的工艺要求和材料特性,在压合机的控制界面上设置合适的压合温度、压力和时间参数,压合温度通常在 180℃ - 220℃之间,压力在 200 - 500psi(磅/平方英寸)之间,时间为 60 - 180 分钟不等,对于普通的多层电路板,可能采用 200℃的温度、300psi 的压力和 120 分钟的时间进行压合;而对于高密度互连(HDI)板等高端产品,由于其结构复杂、线路密度高,可能需要更高的温度(220℃)、更大的压力(400psi)和更长的时间(180 分钟)。
- 还需设置升温速率和降温速率,升温速率一般控制在 2℃ - 5℃/min,降温速率控制在 1℃ - 3℃/min,以避免因温度变化过快导致板材内部产生热应力,从而引起变形、开裂等质量问题。
2、压合执行
- 启动压合机,按照设定好的参数开始进行压合操作,在压合过程中,操作人员要密切监控设备的运行状态,观察温度、压力和时间等参数是否稳定在设定值范围内,如果发现参数出现偏差或异常情况,如温度过高或过低、压力不足等,应立即停止压合操作,查找原因并进行相应的调整和修复后,再重新启动压合过程。
(三)冷却与卸板
1、冷却过程
- 当压合时间到达设定值后,关闭加热系统,让压合机自然冷却至室温,在冷却过程中,要避免对压合机进行任何剧烈的操作或震动,以免影响板材的内部结构和质量,冷却时间可能需要 30 - 60 分钟左右,具体时间取决于板材的尺寸、厚度和环境温度等因素。
2、卸板操作
- 冷却完成后,打开压合机,使用卸板机将压合好的板子平稳地取出,在卸板过程中,要注意轻拿轻放,防止板子因受到外力冲击而产生裂纹或分层现象,将取出的板子放置在指定的周转区域,等待后续的质量检测和加工处理。
三、质量检测与控制
(一)外观检测
1、尺寸测量
- 使用精密的量具,如游标卡尺、千分尺等,对压合后的板子进行尺寸测量,主要测量板子的长、宽、厚度等尺寸参数,检查其是否符合产品的规格要求,对于一块标准的双面电路板,其长度公差可能要求控制在±0.5mm 以内,宽度公差在±0.3mm 以内,厚度公差在±0.2mm 以内。
- 除了整体尺寸外,还需对板上的孔径、槽距等关键尺寸进行测量,确保其精度满足电路设计和装配的要求,一些连接孔的孔径公差可能要求控制在±0.05mm 以内,以保证元器件的顺利安装和焊接。
2、外观缺陷检查
- 在充足的光线下,对板子的外观进行全面检查,查看是否有划伤、凹坑、气泡、分层等缺陷,划伤可能会影响电路板的电气性能和外观质量;凹坑和气泡可能会导致局部线路断裂或绝缘性能下降;分层现象则会严重影响电路板的整体强度和可靠性,对于发现的外观缺陷,要根据其严重程度进行分类记录,并分析产生的原因,采取相应的措施进行改进和预防。
(二)性能检测
1、剥离强度测试
- 采用专用的剥离强度测试设备,对压合后的板材进行铜箔与芯板之间的剥离强度测试,通过施加一定的拉力,测量铜箔从芯板上剥离所需的力大小,以此来评估它们之间的粘结强度,剥离强度应满足产品标准规定的最小值要求,如≥1.0N/cm,如果剥离强度不足,可能会导致铜箔在后续的加工过程中脱落,影响电路板的正常使用。
2、电气性能测试
- 使用阻抗测试仪、耐电压测试仪等设备对电路板进行电气性能测试,检测项目包括线路的电阻、电容、电感以及绝缘电阻、耐压值等参数,对于高频电路板,其线路的阻抗匹配非常重要,否则可能会导致信号反射和衰减;绝缘电阻和耐压值则直接关系到电路板的安全性和可靠性,一般要求绝缘电阻在 10^9Ω以上,耐压值达到 500VDC 以上。
FAQs
问题 1:瀚宇博德压合课在工作中如何确保各层材料之间的精准对位?
答:在叠板操作过程中,利用叠板机的精确定位装置和导向系统来确保各层材料的精准对位,操作人员会在每铺设一层材料后使用滚轮或刮板轻轻压实,并借助一些辅助的定位标记或工具进行检查和微调,保证各层材料的位置准确无误,在设备的日常维护和校准中,也会重点关注这些定位装置的准确性,确保其长期稳定可靠地工作。
问题 2:如果压合后的电路板出现分层现象,可能是什么原因导致的?
答:分层现象的产生可能由多种原因导致,可能是物料本身的问题,如芯板或铜箔的表面处理不当,存在油污、氧化层或其他杂质,影响了粘结效果;压合工艺参数设置不合理也可能导致分层,比如温度过高或过低、压力不足或不均匀、时间过短等;还有可能是在压合过程中设备出现故障或异常情况,如加热板温度不均匀、液压系统压力波动等,在生产过程中需要对每一个环节进行严格的质量控制和监测,以尽量减少分层现象的发生。
小编有话说
瀚宇博德压合课的工作看似只是将几块材料压合在一起,实则蕴含着诸多精细复杂的工序和严格的质量把控要求,从前期物料的精心准备、设备的细致调试,到压合过程中的精准操作和参数控制,再到最后的严格质量检测,每一个环节都至关重要,只有每个步骤都做到严谨认真、一丝不苟,才能生产出高质量、可靠的电路板产品,满足电子行业不断发展的需求,这也体现了瀚宇博德在 PCB 制造领域对品质的执着追求和专业精神,为推动电子产业的发展奠定了坚实的基础。