FMEA即失效模式及影响分析,在半导体中用于识别潜在故障及其对产品的影响。
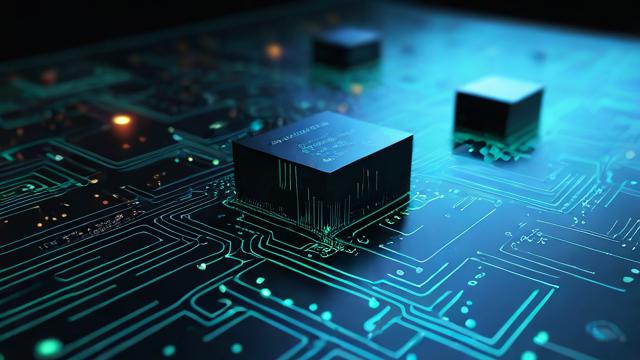
半导体中的FMEA(Failure Mode and Effects Analysis)即失效模式及影响分析,是一种系统化的工程设计辅助工具,旨在通过系统性的分析方法,识别产品开发和生产流程中潜在的失效模式,并评估这些失效模式对产品性能、质量、安全性等方面产生的影响,进而采取相应的优化措施,以避免失效的发生或降低其发生时产生的不良影响,提高整个系统的可靠性,以下是关于半导体中FMEA的详细解释:
1、定义与起源
基本概念:FMEA是一种用来确定潜在失效模式及其原因的分析方法,它聚焦于识别产品或过程中可能出现的故障模式,以及这些故障可能带来的后果,以便提前采取措施加以预防或减轻。
历史背景:FMEA最早诞生于美国,其渊源可以追溯到20世纪40年代的美国军方,当时为了提高武器系统的可靠性,开始运用这一方法来识别和评估潜在的故障模式及其影响,后来在1963年,美国国家航空航天局(NASA)制定了FMECA(失效模式、效应和关键性分析),进一步推动了它的发展,随着时间的推移,FMEA的应用范围不断拓展,逐渐在汽车、航空航天、医疗器械、电子等众多行业中得到了广泛认可和应用。
2、核心目的
识别与评价:帮助识别并评价出产品或过程中潜在的失效模式以及这些失效模式发生后对产品性能的影响,例如在汽车制造过程中,通过FMEA可以分析出发动机某个零部件可能出现的磨损、松动等失效模式,以及由此可能导致的动力下降、油耗增加甚至发动机故障等影响。
探究起因与机理:致力于探究失效模式的起因或机理,进而找出避免或减少这些潜在失效发生的措施,例如在电子产品生产中,若发现某电路焊接处容易出现虚焊这一失效模式,通过分析可以确定是焊接工艺参数不合理或者焊接材料质量不佳等原因导致的,那么就可以针对性地调整工艺参数或者更换优质焊接材料来预防虚焊情况的出现。
分类排序与应对:将全部潜在的失效模式,按照其对产品性能影响的严重程度及其发生的频度加以分类排序,以便采取不同级别的对策,对于严重程度高且发生频度也高的失效模式,会优先投入更多资源去重点解决;而对于影响较小、发生概率低的失效模式,则可以适当安排后续的改进计划。
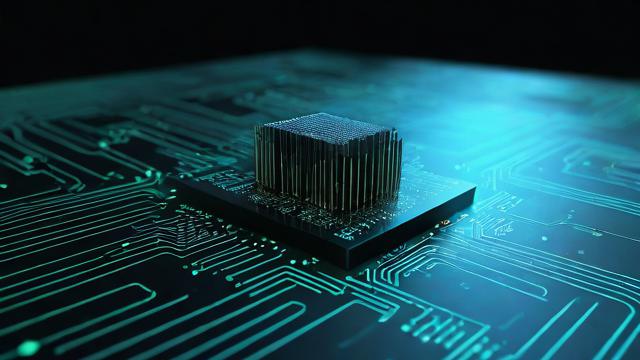
3、重要作用
风险识别与预防:通过对产品或流程各个环节进行系统且全面的分析,从设计、制造、装配,再到使用、维护等多个维度,来找出潜在的风险,并提前采取相应的预防措施,例如在汽车制造行业中,一款新车型的研发阶段,运用FMEA可以分析出发动机的冷却系统可能存在冷却液泄漏这一潜在风险,以及刹车系统可能存在刹车片过度磨损后未能及时提醒更换的隐患等,从而提前知晓并采取预防措施。
影响量化评估:能够对不同故障模式产生的影响进行量化处理,让企业清晰地了解每个故障模式的严重程度,以便有针对性地制定预防举措,例如在医疗器械行业,心脏起搏器出现起搏信号不稳定的故障模式严重程度可评定为很高,而设备外壳出现轻微划痕这种故障模式严重程度则较低。
指导措施制定:不仅能精准确定需要采取的预防措施,还能详细指导企业该如何去实施这些措施,涵盖了改进设计、更换材料、优化工艺等多个关键方面,比如在食品加工行业,某罐头生产企业通过FMEA分析发现罐头密封不严这一潜在失效模式后,可以从改进设计、更换材料、优化工艺等多个方面制定具体措施来解决问题。
促进团队协作与沟通:实施通常需要跨部门合作来完成,在这个过程中,能够有效提高团队的凝聚力、合作能力,并且促进企业内部的交流沟通,各个部门通过定期的FMEA会议、小组讨论等形式,充分交流各自专业领域的知识和见解,打破部门壁垒,提升整体运作效率。
助力持续改进:作为一种持续性的质量工具,能够促使企业在产品或流程的各个阶段都保持警惕,不断优化以适应市场和客户需求的变化,例如在互联网软件行业,一款社交软件通过FMEA分析发现用户登录环节偶尔会出现卡顿的故障模式后,开发团队可以针对此问题进行持续改进。
4、执行步骤
确定分析范围:明确要分析的产品或过程。
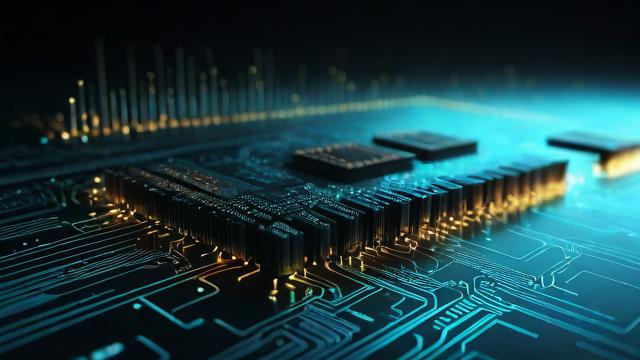
识别潜在失效模式:列出所有可能的失效模式。
分析失效影响:评估每个失效模式对产品或过程的影响。
确定失效原因:找出每个失效模式的可能原因。
评估风险:根据失效模式的严重性、发生频率和可检测性,评估风险优先级(RPN)。
制定改进措施:针对高风险的失效模式,制定改进措施。
实施和验证:实施改进措施,并验证其有效性。
FMEA在半导体领域扮演着至关重要的角色,它不仅有助于提升产品质量和可靠性,还能降低成本、增强客户满意度,是半导体企业不可或缺的风险管理工具。