精益管理中的浪费包括等待、搬运、不良、动作、加工、库存、管理和制造过量(过早)等八种,这些浪费现象会导致生产效率低下和成本增加。
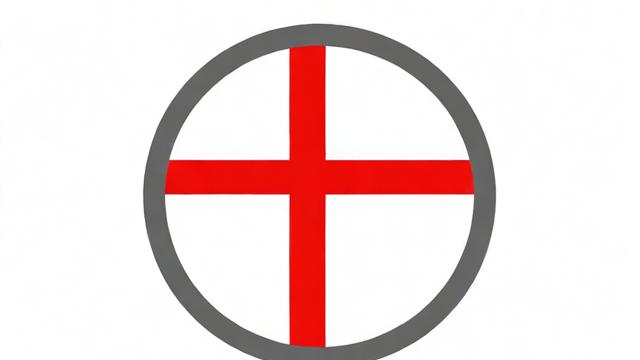
精益生产中的浪费是指任何不增加产品或服务价值的活动,这些浪费不仅会导致生产成本的增加,还可能降低生产效率,影响产品质量和客户满意度,以下是精益生产中常见的八种浪费:
1、等待的浪费:指由于原材料供应中断、操作不平衡、生产计划不当等原因,员工无法为客户创造价值的等待时间,这种浪费常见于生产线上的设备故障等待修理、质量检查等待结果等场景。
2、搬运的浪费:在处理过程中不产生附加值的行为,如堆放、摆放、移动、分拣等,它造成货物移动所需的空间浪费、时间浪费和人力工具浪费,不仅增加了搬运成本,还可能导致货物在搬运过程中丢失或损坏。
3、不良的浪费:企业发生次品时,需要投入时间、人力、物力进行处理,这种浪费具体包括员工工作时间的损失、设备的损失、材料的损失、额外修理的损失、鉴定的损失、额外检查的损失、不良品的损失到报废、减价处理的损失、延误的损失和工厂信誉的损失等。
4、动作的浪费:由于工位、物品、设备等布置不合理,以及工具和操作方法使用不当而造成的浪费,员工的劳动可以分为创造附加值的作业和不创造附加值的作业,后者即为动作浪费。
5、加工的浪费:机械加工操作中所有与工程进度和加工精度无关的不必要的加工,这种浪费会增加生产时间和成本,同时也会导致能源和资源的浪费。
6、库存的浪费:原材料、在制品、成品等超过制造过程中所需的最适当数量,库存过多会导致资金占用、利息和管理成本增加,同时也可能隐藏生产过程中的问题。
7、管理的浪费:员工积极性不高、自主管理能力不强、管理制度不健全等原因造成的浪费,管理成本是企业成本构成的重要组成部分,管理层必须按“理”行事,控制成本,减少浪费。
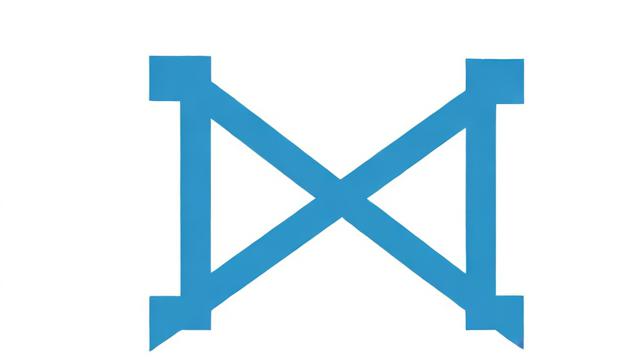
8、制造过多的浪费:生产超额完成任务,而过多地制造和提前生产所造成的浪费,过早制造过多,导致产成品生产过剩,在制品堆积生产场地和仓库,增加了制造场地和库存所需面积,产生了无用的运输和利息支出。
通过识别和消除这些浪费,企业可以优化生产流程,提高生产效率,降低成本,并提升产品质量和客户满意度,采用拉动式生产系统来避免过量生产,优化生产布局和流程以减少运输和动作浪费,加强质量管理以降低次品率等。
以下是关于精益生产的两个常见问题及其解答:
Q1: 精益生产中的“七大浪费”具体指的是什么?
A1: 精益生产中的“七大浪费”指的是等待的浪费、搬运的浪费、不良的浪费、动作的浪费、加工的浪费、库存的浪费和管理的浪费,这些浪费都是不增加产品或服务价值的活动,需要被识别和消除以提高生产效率和降低成本。
Q2: 如何有效实施精益生产以减少浪费?
A2: 有效实施精益生产以减少浪费需要采取一系列措施,包括培训和教育员工了解精益理念和方法,观察和检查生产线以发现浪费现象,对生产流程进行改进和优化以消除浪费,鼓励员工积极参与并提出改进建议,以及定期评估和归纳推广活动的效果,通过持续改善和追求完美,企业可以逐步实现精益生产的目标。
小编有话说:精益生产是一种以客户为中心的生产哲学,它要求企业管理者和员工都站在不断消除浪费、持续改善的立场上重新审视每一个生产环节,通过识别和消除浪费,我们可以优化生产流程,提高生产效率,降低成本,并提升产品质量和客户满意度,让我们共同努力,将精益生产的理念和方法应用到实际工作中去,为企业创造更大的价值!