精益改善运用消除浪费、持续改进、价值流分析、标准化作业和尊重人的原则。
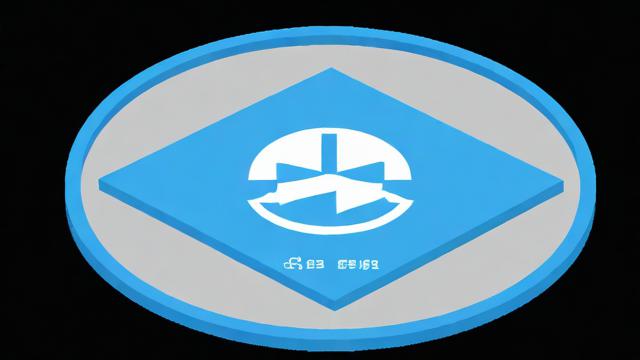
精益改善是一种旨在通过消除浪费、提高效率和质量的管理方法,广泛应用于制造业和其他行业,精益改善运用多个原则来实现这些目标,以下是一些关键原则及其详细解释:
1. 价值定义(Value Definition)
定义客户价值:从客户的角度出发,明确什么是有价值的产品或服务,只有满足客户需求的活动才是有价值的。
2. 价值流映射(Value Stream Mapping)
识别并绘制整个价值流:通过绘制当前状态的价值流图,识别出增值活动和非增值活动(浪费),这有助于找到改进的机会。
流动(Flow)
确保工作顺畅流动:减少中断和等待时间,使工作流程连续不断,通过优化流程布局和设备配置,实现物料和信息的自由流动。
拉动(Pull)
按需生产:根据客户的需求拉动生产和供应,而不是推动,这种方法可以减少库存和过度生产的风险。
尽善尽美(Perfection)
持续改进:追求完美,不断寻找改进的机会,鼓励员工提出改进建议,并通过小步快跑的方式逐步实现改进。
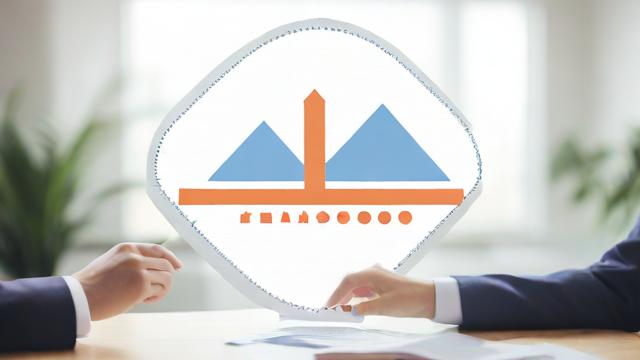
6. 消除浪费(Eliminate Waste)
识别并消除七种浪费:包括过剩生产、等待时间、运输、过度加工、库存、运动和缺陷,通过消除这些浪费,可以显著提高效率和降低成本。
7. 标准化作业(Standardized Work)
建立标准操作程序:制定详细的作业指导书,确保每个步骤都按照最佳实践执行,这有助于保持一致性和高质量。
8. 尊重人(Respect for People)
关注员工的发展和参与:尊重员工的意见和贡献,鼓励团队合作和持续学习,通过培训和发展计划,提升员工的技能和能力。
9. 可视化管理(Visual Management)
使用视觉工具进行管理:通过看板、图表和其他视觉工具,使问题显而易见,方便及时发现和解决问题。
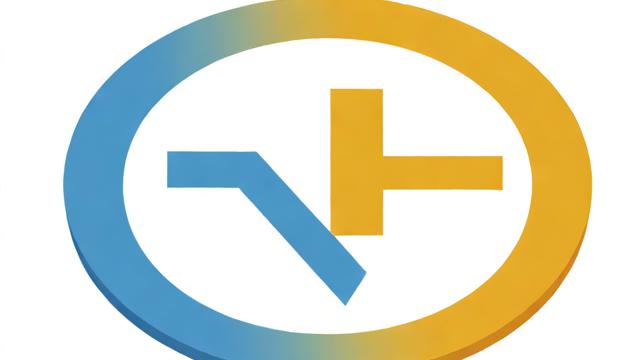
10. 快速换模(Quick Changeover)
缩短换模时间:通过优化设备和流程,减少换模时间,提高设备的利用率和生产效率。
自动化(Automation)
智能自动化:在适当的地方引入自动化技术,但前提是已经消除了浪费,自动化应该是为了提高效率和质量,而不是简单地替代人力。
持续改进(Kaizen)
小步快跑:通过持续的小改进积累大的成果,鼓励员工在日常工作中发现问题并提出改进建议。
表格示例:精益改善原则及其应用
原则 | 描述 | 应用场景 |
价值定义 | 明确客户需求,确定有价值的活动 | 产品开发、服务设计 |
价值流映射 | 绘制当前状态的价值流图,识别浪费 | 流程分析、改进项目 |
流动 | 确保工作顺畅流动,减少等待时间 | 生产线布局、供应链管理 |
拉动 | 根据客户需求拉动生产和供应 | 库存管理、订单处理 |
尽善尽美 | 持续改进,追求完美 | 所有业务流程 |
消除浪费 | 识别并消除七种浪费 | 成本控制、效率提升 |
标准化作业 | 建立标准操作程序,确保一致性 | 质量控制、培训 |
尊重人 | 关注员工发展,鼓励参与 | 人力资源管理、团队建设 |
可视化管理 | 使用视觉工具进行管理 | 现场管理、问题解决 |
快速换模 | 缩短换模时间,提高设备利用率 | 设备维护、生产线切换 |
自动化 | 引入智能自动化技术 | 制造过程、物流管理 |
持续改进 | 通过小步快跑实现大成果 | 日常运营、项目管理 |
相关问答FAQs
Q1: 精益改善中的“拉动”原则具体是什么意思?
A1: “拉动”原则是指根据客户的需求来驱动生产和供应,而不是基于预测进行生产,这意味着只有在客户下单后,才开始生产和配送,这种方式可以减少库存积压和过度生产的风险,提高资源的利用效率,丰田汽车公司就采用了拉动式的生产方式,通过看板系统实时传递需求信息,确保每个环节只生产所需的数量。
Q2: 如何有效地实施“标准化作业”原则?
A2: 实施“标准化作业”原则需要以下几个步骤:
1、识别关键流程:确定哪些流程对质量和效率影响最大。
2、制定标准操作程序(SOP):为每个关键流程编写详细的操作指南,包括步骤、工具、时间和质量标准。
3、培训员工:确保所有相关人员都熟悉并理解SOP,并进行必要的培训。
4、执行和监督:严格按照SOP执行操作,并定期检查执行情况,确保一致性和高质量。
5、持续改进:根据实际情况和反馈,不断优化和完善SOP,以适应变化的需求和技术。
小编有话说
精益改善不仅仅是一种管理工具,更是一种思维方式和文化,它要求我们始终以客户为中心,不断寻找改进的机会,消除浪费,提高效率和质量,通过遵循上述原则,企业可以在竞争激烈的市场中脱颖而出,实现可持续发展,希望这篇文章能帮助你更好地理解和应用精益改善的原则,为企业带来实实在在的效益,如果你有任何疑问或需要进一步的帮助,请随时联系我们!