动作的浪费指的是在生产过程中,那些不增加产品价值、不必要或多余的动作和操作。
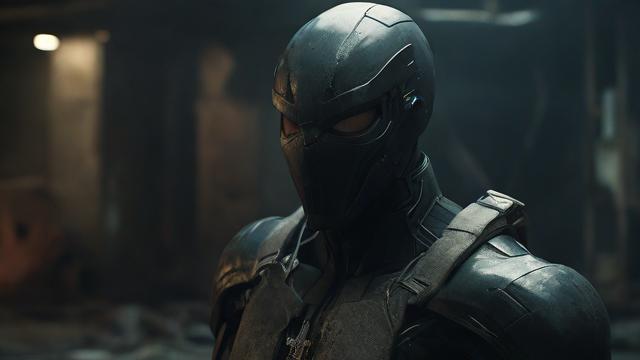
动作的浪费,通常指的是在生产和工作过程中,那些不增值且不必要的动作或步骤,这些动作虽然看似忙碌,但实际上并未对最终产品或服务的质量、功能或价值产生任何正面影响,它们可能是由于流程设计不合理、员工操作习惯不佳、设备布局不当等多种原因造成的,动作的浪费不仅增加了生产成本,降低了工作效率,还可能影响员工的士气和工作满意度。
为了更直观地理解动作的浪费,我们可以将其细分为几个常见的类型,并通过表格形式进行展示:
动作浪费类型 | 描述 | 示例 |
过度加工 | 对产品或工件进行超出必要范围的加工处理 | 对一个只需简单打磨的产品进行精细雕刻 |
多余动作 | 员工在工作中进行的非必要的身体移动或操作 | 频繁弯腰取放工具,而工具本可以放在更顺手的位置 |
等待时间 | 员工或设备在生产过程中因等待而闲置的时间 | 上一道工序未完成,导致下一道工序无法开始 |
寻找时间 | 员工在寻找工具、材料或信息时所花费的时间 | 仓库物品摆放混乱,员工需要花费大量时间寻找所需物品 |
搬运浪费 | 对产品或物料进行不必要的移动或搬运 | 将半成品在不同车间之间多次转运,而非直接送达最终加工地点 |
库存浪费 | 过多的原材料、半成品或成品库存占用空间和资金 | 过度生产导致的库存积压,或采购过量的原材料 |
不合格品 | 生产过程中产生的废品、次品或需要返工的产品 | 由于操作不当或设备故障导致的产品质量问题 |
这些动作浪费不仅消耗了企业的资源,还可能导致生产效率低下、成本增加、交货期延误等问题,识别并消除动作浪费是提升企业竞争力的关键之一。
我们通过两个相关问答FAQs来进一步探讨动作浪费的问题:
Q1: 如何有效识别生产过程中的动作浪费?
A1: 识别动作浪费需要细致入微的观察和分析,可以通过流程图或作业分析来梳理整个生产过程,找出每个环节中的非增值活动,利用5S(整理、整顿、清扫、清洁、素养)等现场管理方法,改善工作环境,减少寻找和等待时间,还可以采用精益生产中的“三现主义”(现场、现物、现实)原则,即亲临现场查看实际情况,对具体事物进行直接观察和分析,以更准确地识别浪费所在。
Q2: 消除动作浪费有哪些常用方法?
A2: 消除动作浪费的方法多种多样,包括但不限于以下几种:一是流程优化,通过重新设计工作流程,减少不必要的步骤和环节;二是标准化作业,制定明确的操作规范,减少员工操作的随意性和差异性;三是引入自动化设备,替代人工进行重复性、低附加值的工作;四是持续培训员工,提高他们的技能水平和工作效率;五是实施看板管理、准时制生产(JIT)等先进管理方法,减少库存浪费和等待时间。
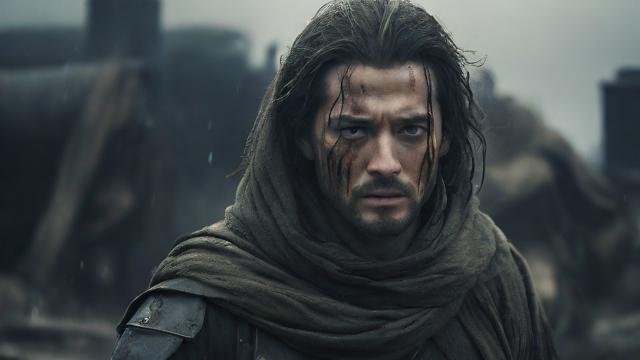
小编有话说:在追求高效与精益的时代背景下,识别并消除动作浪费已成为企业提升竞争力、实现可持续发展的重要途径,这不仅仅是一场关于技术和方法的革命,更是一次对企业管理模式、员工思维方式的深刻变革,让我们共同努力,从细微处入手,不断挖掘潜力,为企业创造更大的价值,也期待每一位员工都能积极参与到这一过程中来,共同推动企业的持续进步与发展。