工厂TPM即全面生产维护,旨在通过全员参与,提高设备综合效率,实现零事故、零故障、零缺陷的目标。
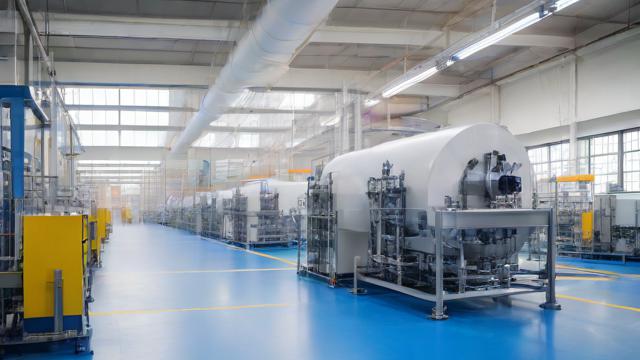
TPM(Total Productive Maintenance,全面生产维护)是一种全员参与的生产维护方法,旨在通过提高设备效率和员工素质来提升企业整体的生产效率,以下是对工厂TPM的详细解释:
1、定义与目标
定义:TPM是一种以设备综合效率最大化为目标的管理系统,它涉及全体员工的参与,包括从高层管理人员到一线操作工人。
目标:追求零事故、零故障、零缺陷的目标,通过预防性维护减少设备的非计划停机时间,从而提高生产效率和产品质量。
2、核心要素与支柱活动
小组活动:通过小组活动推进TPM的实施,每个小组负责特定区域的设备维护和管理,确保设备维持在最佳运行状态。
5S活动:5S是整理、整顿、清扫、清洁、素养的简称,是TPM的基础活动,为现场管理提供标准化的操作环境。
教育培训:持续的员工教育和培训是TPM成功的关键,确保每位员工都具备必要的技能和知识来参与维护活动。
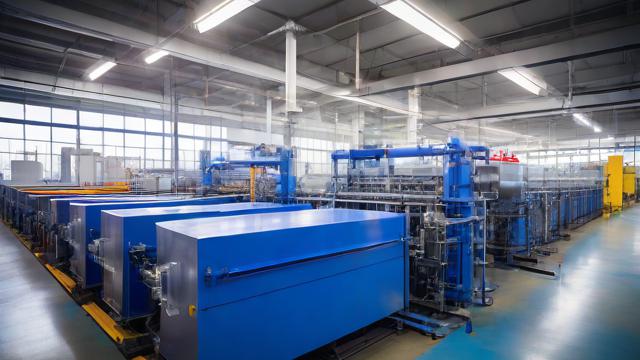
自主管理:鼓励员工进行自主管理,提高他们对设备维护的责任感和主动性。
专业保全:设备部门的专业保全活动,包括预防性维护和故障诊断,以提高设备的可靠性和性能。
事务革新:管理间接部门的事务革新活动,提高工作效率和服务质量,支持生产部门的TPM活动。
情报管理:技术部门通过情报管理活动,掌握产品设计和设备设计的必要信息,以支持TPM的实施。
安全管理:安全是TPM活动中的首要任务,所有活动都必须确保员工的安全。
品质保全:品质部门的品质保全活动,确保产品和服务的质量满足标准要求。
3、实施步骤与策略
先期设备管理:从设备需求提出到设备采购、安装调试、验收投入使用的管理过程,确保新设备的可靠度和保养能力。
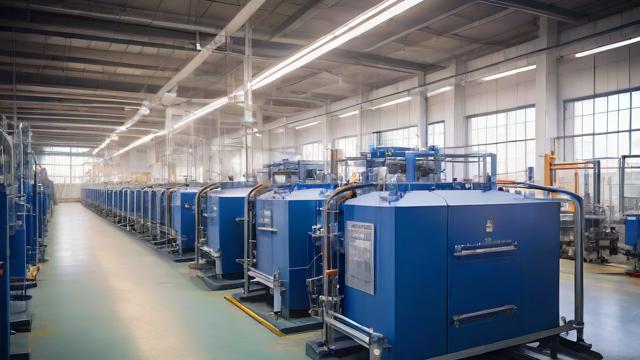
动态管理:TPM管理是一个动态的过程,需要不断地根据企业发展和市场变化进行调整和优化。
开放性:TPM管理需要与企业的其他管理体系相互配合,形成一个完整的企业管理生态系统。
TPM不仅仅是一种设备维护的方法,它是一种全面的生产管理哲学,通过全员参与和系统化的管理,实现生产效率和产品质量的全面提升,企业在实施TPM时,需要结合自身的实际情况,制定合适的策略和步骤,确保TPM活动的有效性和可持续性。