精益提升是通过消除浪费、优化流程和持续改进,以提高生产效率和质量的管理方法。
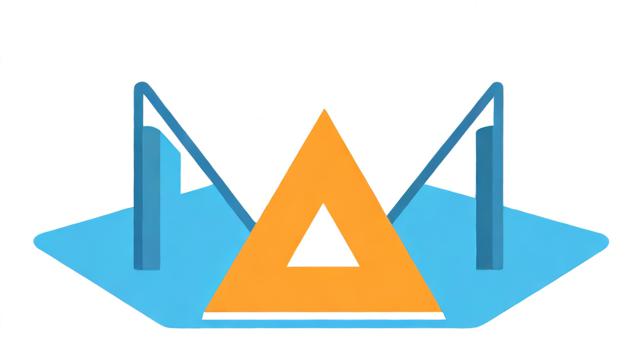
精益提升是一种旨在通过消除浪费、优化流程和提高效率来提升组织绩效的管理理念和方法,它起源于日本的丰田生产系统,并逐渐在全球范围内得到广泛应用,精益提升的核心目标是在不增加成本的前提下,通过持续改进和创新,实现更高的生产效率和更好的产品质量。
精益提升的基本原则包括:
1、价值:明确客户需求,专注于创造价值的活动。
2、价值流:分析整个生产过程,识别并消除浪费。
3、流动:确保生产过程顺畅,减少停滞和等待时间。
4、拉动:根据客户需求进行生产,避免过度生产。
5、尽善尽美:持续改进,追求卓越。
6、尊重人:关注员工的成长和发展,激发员工的潜能。
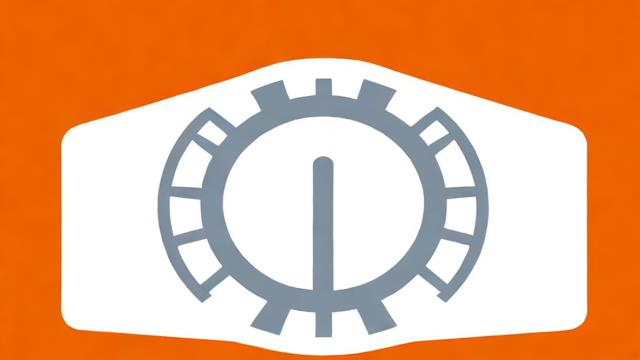
7、可视化管理:通过直观的方式展示生产和管理信息,便于发现问题和改进。
精益提升的实施步骤通常包括:
1、确定目标:明确要解决的问题和改进的目标。
2、现状分析:收集数据,了解当前的生产过程和问题所在。
3、制定计划:根据现状分析结果,制定改进措施和实施计划。
4、执行计划:按照制定的计划进行改进措施的实施。
5、检查效果:对实施结果进行检查,评估改进效果。
6、标准化:将有效的改进措施纳入标准操作程序,确保持续改进。
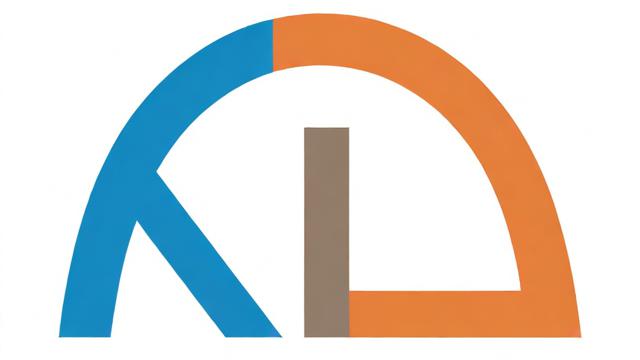
7、持续改进:不断循环上述步骤,实现持续改进和提升。
精益提升在不同领域都有广泛的应用,如制造业、服务业、医疗保健等,通过实施精益提升,组织可以实现以下好处:
1、提高生产效率:消除浪费,优化流程,提高生产效率。
2、降低成本:减少不必要的支出,降低生产成本。
3、提高产品质量:通过持续改进,提高产品质量和客户满意度。
4、增强竞争力:提高组织的整体绩效,增强市场竞争力。
5、提升员工满意度:关注员工的成长和发展,提高员工的工作满意度和忠诚度。
相关问答FAQs:
1、什么是精益提升?
答:精益提升是一种旨在通过消除浪费、优化流程和提高效率来提升组织绩效的管理理念和方法,它起源于日本的丰田生产系统,并逐渐在全球范围内得到广泛应用。
2、精益提升的核心原则是什么?
答:精益提升的核心原则包括价值、价值流、流动、拉动、尽善尽美、尊重人和可视化管理,这些原则共同构成了精益提升的基础框架,指导组织进行持续改进和创新。