精益TPM是一种融合了精益生产方法的管理工具,旨在通过全员参与和持续改进,提高设备的综合效率和可靠性。
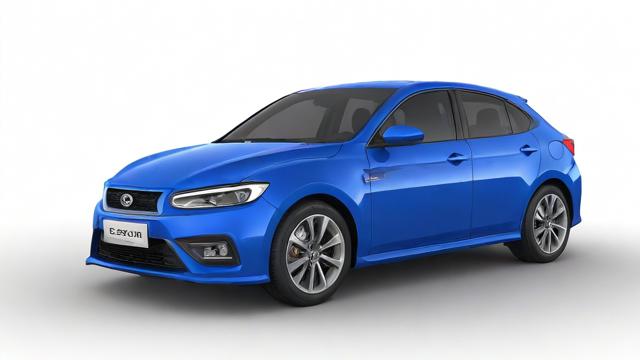
精益TPM(Total Productive Maintenance,全面生产维护)是一种融合了精益生产和TPM(全面生产维护)理念的管理方法,旨在通过全员参与、持续改进的方式,最大化地提升设备综合效率(OEE),减少浪费,确保生产系统的稳定性和高效性,以下是关于精益TPM的详细解释:
一、核心理念
1、全员参与:强调从管理层到一线员工,每个人都应成为设备维护和生产优化的主体,共同为提升生产效率和产品质量努力。
2、预防为主:通过定期维护、故障预测等手段,提前发现并解决潜在问题,避免设备故障导致的生产中断和损失。
3、持续改进:鼓励员工提出改善建议,不断寻找并消除生产过程中的浪费,实现生产流程的持续优化。
4、价值导向:明确生产过程中的价值流,消除非增值活动,确保每一道工序都能为客户创造价值。
二、实施步骤
精益TPM的实施通常包括以下几个步骤:
步骤 | 描述 |
现状评估 | 对现有生产系统进行全面的评估,识别存在的浪费、故障频发点及瓶颈环节。 |
目标设定 | 基于现状评估结果,设定具体的改善目标,如提高设备综合效率、降低故障率、缩短换模时间等。 |
培训与教育 | 组织全员参与精益TPM管理知识的培训,提升员工对精益TPM管理的认识和理解,激发其参与改善的积极性。 |
制定计划 | 根据改善目标,制定详细的实施计划,明确责任分工、时间节点和预期成果。 |
执行与监控 | 按照计划执行改善措施,同时建立监控机制,确保改善措施的有效实施和及时调整。 |
评估与反馈 | 定期对改善效果进行评估,归纳经验教训,形成闭环管理,为下一轮改善提供依据。 |
三、关键要素
精益TPM的成功实施依赖于以下关键要素:
要素 | 描述 |
5S管理 | 作为精益TPM管理的基础,5S有助于营造整洁有序的工作环境,为设备维护和生产优化提供有力支持。 |
自主维护 | 鼓励员工参与设备的日常维护,培养员工的“我的设备我负责”的意识,减少设备故障的发生。 |
专业维护 | 建立专业的设备维护团队,负责设备的定期检修、故障排查和预防性维护,确保设备的稳定运行。 |
持续改进机制 | 建立持续改进的文化和机制,鼓励员工提出改善建议,形成全员参与、持续改进的良好氛围。 |
信息化支撑 | 利用现代信息技术手段,如物联网、大数据等,实现设备状态的实时监控和数据分析,为精益TPM管理提供有力支撑。 |
四、成功案例分享
某汽车制造企业在引入精益TPM管理后取得了显著成效,该企业首先通过现状评估识别出生产线上的多个瓶颈环节和浪费点,随后制定了详细的改善计划并组织全员参与的培训活动,在实施过程中注重自主维护与专业维护的结合,建立了完善的设备维护体系,并利用信息化手段实现了设备状态的实时监控和数据分析,经过一年的努力,该企业的设备综合效率提高了20%,故障率降低了30%,生产周期缩短了15%,产品质量也得到了显著提升,这一成功案例充分证明了精益TPM管理在提升企业竞争力方面的巨大潜力。
五、FAQs
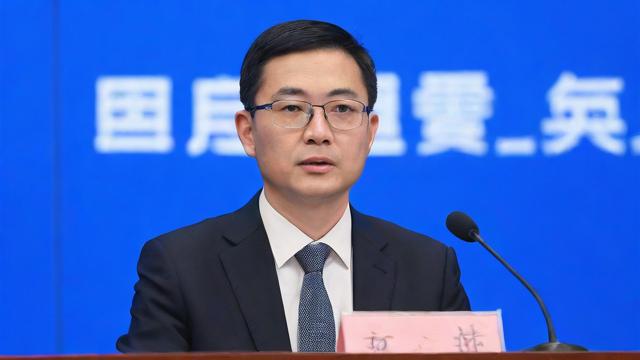
Q1: 精益TPM与传统TPM有何区别?
A1: 精益TPM在传统TPM的基础上融入了精益生产的理念和方法工具,更加注重全员参与、持续改进和价值导向,它不仅关注设备的维护和管理还强调生产过程中的浪费消除和效率提升。
Q2: 如何有效推进精益TPM的实施?
A2: 推进精益TPM的实施需要企业上下一心持之以恒地推进,首先进行全面的现状评估明确改善目标;其次组织全员参与的培训活动提升员工认识;再次制定详细的实施计划并严格执行;最后定期评估改善效果并形成闭环管理为下一轮改善提供依据,同时还需要建立持续改进的文化和机制以及信息化支撑系统来保障精益TPM管理的顺利实施。
六、小编有话说
精益TPM作为一种先进的管理理念和方法对于提升企业生产效率、降低生产成本、提高产品质量具有重要意义,然而其实施并非一蹴而就而是需要企业上下一心持之以恒地推进,在实施过程中我们需要注重全员参与、持续改进和价值导向的理念将精益生产和TPM的优势充分发挥出来以实现生产系统的高效稳定运行和企业竞争力的不断提升。