全员生产维护(Total Productive Maintenance,简称TPM)是一种以设备综合效率最大化为目标的维修和维护体系。
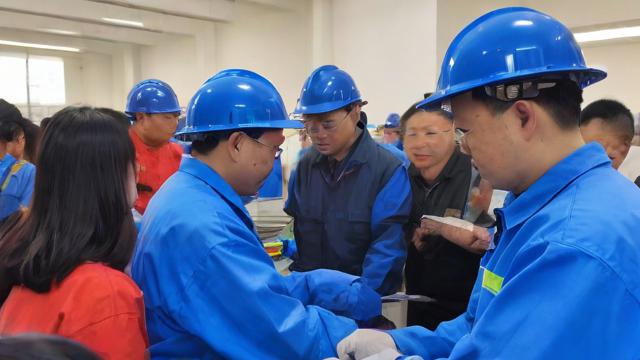
全员生产维护(Total Productive Maintenance,简称TPM)是一种全面的设备管理和维护策略,旨在通过全体员工的参与和持续改进,实现设备的高效运行、减少故障停机时间,并提升生产效率,TPM强调预防性维护,而不仅仅是事后修理,其核心理念是“我的设备我维护”。
TPM的核心要素
1、自主维护:这是TPM的基础,要求操作人员对自己的设备进行日常维护和检查,包括清洁、润滑、紧固等基本工作,通过自主维护,员工可以及时发现设备的小问题并解决,避免小问题演变成大故障。
2、专业维护:虽然自主维护是基础,但专业的维护团队仍然不可或缺,他们负责更复杂的维修任务,如更换零部件、调试设备等,专业维护与自主维护相辅相成,共同确保设备的稳定运行。
3、预防性维护:TPM强调预防胜于治疗,因此会制定详细的预防性维护计划,定期对设备进行检查和保养,以延长设备的使用寿命并减少突发故障。
4、持续改进:TPM是一个持续改进的过程,鼓励员工提出改进建议,不断优化维护流程和设备性能,通过小步快跑的方式,逐步提升整体效率。
5、培训与教育:为了实施TPM,企业需要对员工进行全面的培训,包括设备知识、维护技能、团队协作等方面,培训不仅提升了员工的技能水平,还增强了他们的责任感和归属感。
TPM的实施步骤
1、准备阶段:明确TPM的目标和意义,组建实施团队,制定实施计划。
2、初始清洁:组织员工对设备进行全面的清洁,发现并记录设备存在的问题。
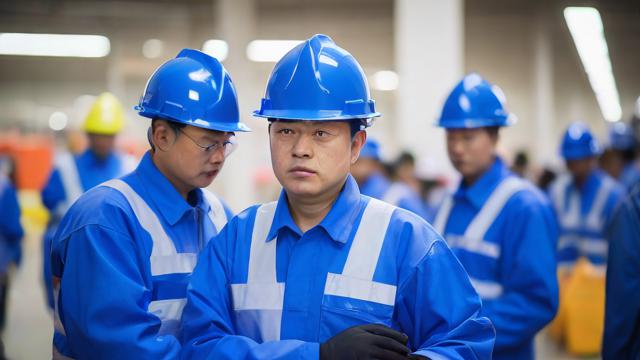
3、问题解决:针对初始清洁中发现的问题,制定解决方案并实施。
4、制定标准:根据问题解决的经验,制定设备维护的标准操作程序(SOP)。
5、培训与教育:对员工进行TPM理念和技能的培训。
6、持续改进:建立持续改进机制,鼓励员工提出改进建议,不断优化维护流程。
TPM的效果评估
TPM的效果可以通过多个指标来评估,包括但不限于:
设备可用率:衡量设备在需要时的可用状态。
故障停机时间:统计因设备故障导致的停机时间。
维护成本:比较实施TPM前后的维护成本变化。
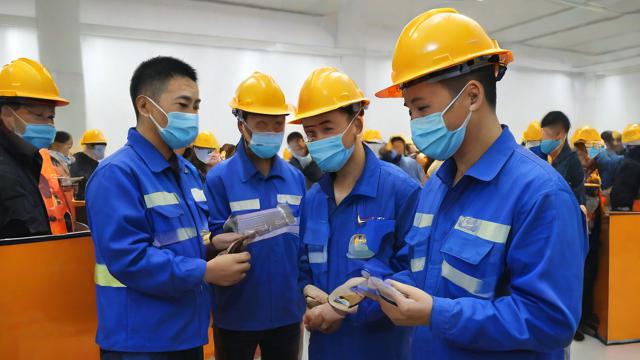
生产效率:观察实施TPM后生产效率的提升情况。
员工满意度:调查员工对TPM实施的满意度和参与度。
表格示例:TPM实施前后对比
指标 | 实施前 | 实施后 | 变化 |
设备可用率 | 80% | 95% | +15% |
故障停机时间 | 每月50小时 | 每月10小时 | -80% |
维护成本 | 每年100万元 | 每年70万元 | -30% |
生产效率 | 每小时10件 | 每小时15件 | +50% |
员工满意度 | 70% | 90% | +20% |
相关问答FAQs
Q1: TPM是否只适用于制造业?
A1: 不完全是,虽然TPM最初是在制造业中发展起来的,但其核心理念——全员参与、持续改进、预防性维护——同样适用于其他行业,如服务业、建筑业等,任何需要设备维护和管理的行业都可以从TPM中受益。
Q2: 实施TPM是否需要高昂的成本?
A2: 实施TPM的初期可能需要一定的投入,包括培训费用、设备改造费用等,但从长远来看,TPM能够显著降低维护成本、提高生产效率、减少故障停机时间,从而带来可观的经济效益,可以说TPM是一项值得投资的长期战略。
小编有话说
全员生产维护(TPM)不仅仅是一种设备管理策略,更是一种企业文化和管理哲学,它强调的是全员参与、持续改进和预防性维护的重要性,通过实施TPM,企业可以建立起一个高效、稳定、可靠的生产系统,为企业的持续发展奠定坚实的基础,实施TPM并非一蹴而就的事情,它需要企业上下一心、持之以恒地努力,但只要我们坚持下去,就一定能够收获满满的回报。