快换模是一种旨在显著减少设备或生产线从一种产品切换到另一种产品所需时间的技术和方法。
什么是快换模?
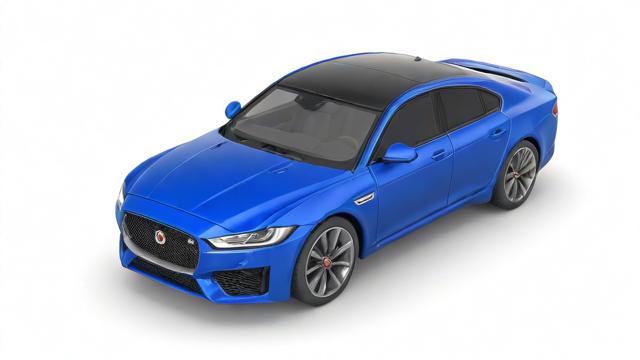
快换模(Quick Changeover,简称QCO),又称快速换模或SMED(Single Minute Exchange of Die),是一种旨在减少设备从生产一种产品切换到另一种产品所需时间的技术和方法,这一概念最早由工业工程师Shigeo Shingo在20世纪60年代提出,是丰田生产方式(Toyota Production System, TPS)中的重要组成部分,快换模技术通过优化换模流程、标准化操作步骤、使用专用工具和设备等手段,将原本可能需要数小时甚至更长时间的换模过程缩短至几分钟甚至几秒钟,从而显著提升生产效率、降低生产成本,并增强企业的市场竞争力。
快换模的基本原理
快换模的核心思想是将换模过程分解为一系列可重复、可预测的步骤,并通过持续改进消除其中的浪费和无效作业,其基本原理包括以下几个方面:
1、观察与记录:首先对当前的换模流程进行全面细致的观察,记录每一个步骤所需的时间和资源消耗。
2、区分内部与外部作业:将换模过程中必须在设备停机状态下完成的内部作业(如拆卸模具、安装新模具等)与可以在设备运行期间同时进行或预先完成的外部作业(如准备工具、调整参数等)区分开来。
3、转化内部作业为外部作业:尽可能将内部作业转化为外部作业,以减少设备的实际停机时间。
4、简化与标准化:简化换模步骤,去除不必要的动作,制定并执行标准化的操作流程。
5、使用快速夹具与工具:采用快速夹紧装置、预调整装置等专用工具,减少手动调整时间和劳动强度。
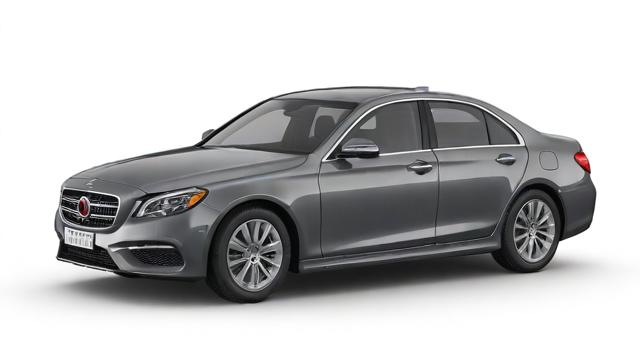
6、持续改进:建立持续改进机制,定期回顾换模流程,寻找进一步缩短换模时间的机会。
实施快换模的步骤
实施快换模通常遵循以下步骤:
1、现状分析:收集并分析当前换模流程的数据,识别瓶颈和浪费环节。
2、目标设定:根据企业实际情况和需求,设定具体的换模时间缩减目标。
3、方案设计:基于现状分析和目标设定,设计具体的快换模实施方案,包括流程优化、工具改进、人员培训等。
4、实施与监控:按照设计方案实施快换模项目,同时建立监控机制,确保各项措施得到有效执行。
5、评估与反馈:项目实施后,对换模时间、生产效率、成本节约等关键指标进行评估,并根据反馈结果进行调整优化。
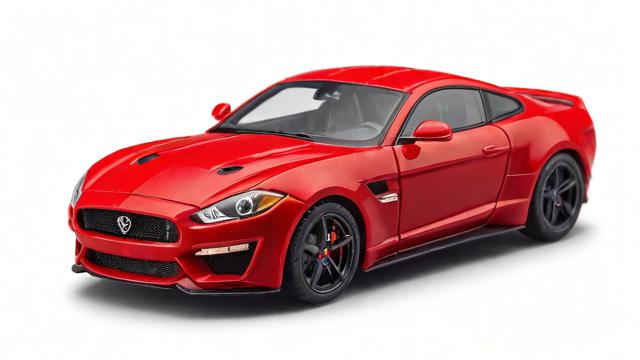
快换模的优势
提高生产效率:显著缩短换模时间,增加有效生产时间,提升整体生产效率。
降低生产成本:减少停机时间和人工成本,降低单位产品的生产成本。
增强灵活性:快速响应市场需求变化,轻松应对小批量、多品种的生产需求。
提升产品质量:标准化的操作流程有助于减少人为错误,提高产品质量稳定性。
激发员工创新:鼓励员工参与换模流程的优化与改进,提升团队协作能力和创新能力。
快换模在不同领域的应用
快换模技术广泛应用于汽车制造、电子组装、塑料制品、金属加工等多个行业,尤其是在需要频繁更换模具或工具的生产过程中效果尤为显著,在注塑成型行业中,通过实施快换模技术,企业能够在短时间内完成不同产品的生产切换,满足多样化的市场需求。
相关问答FAQs
Q1: 快换模只适用于大批量生产吗?
A1: 不完全是,虽然快换模在大批量生产中能显著提高效率,但它同样适用于小批量、多品种的生产环境,通过减少换模时间,企业可以更灵活地应对市场需求的变化,实现按需生产,减少库存积压。
Q2: 实施快换模是否需要高昂的投资?
A2: 实施快换模确实可能需要一定的初期投资,主要用于购买快速夹具、预调整装置等专用工具以及进行员工培训,这些投资通常能在较短时间内通过提高生产效率、降低成本收回,许多快换模技术并不需要昂贵的设备,而是通过优化流程、标准化操作来实现的,因此企业可以根据自身情况选择适合的实施策略。
小编有话说
快换模作为一种先进的生产管理技术,不仅能够帮助企业提高生产效率、降低成本,还能增强企业的市场竞争力和适应能力,在当前市场环境下,客户需求日益多样化、个性化,快速响应市场变化成为企业生存和发展的关键,学习和掌握快换模技术,对于希望提升生产管理水平的企业来说,无疑是一项值得投资的重要举措,实施快换模并非一蹴而就的过程,它需要企业管理层的支持、员工的积极参与以及持续的改进和优化,才能真正发挥出快换模技术的巨大潜力,为企业创造更大的价值。