生产现场改善是提高生产效率,优化工作流程,减少浪费,提升产品质量的过程。
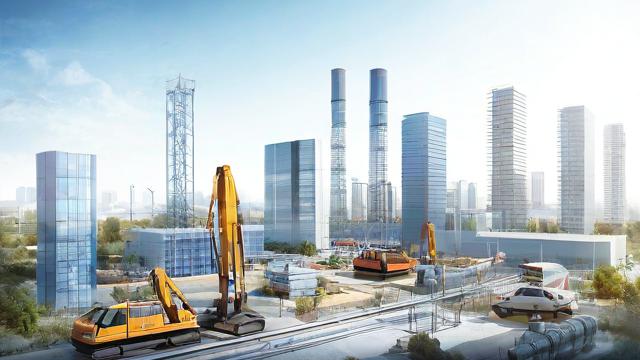
生产现场改善是企业在生产过程中,通过系统化的方法和技术手段,对生产现场进行优化和改进,以提升生产效率、降低成本、确保产品质量,并提高客户满意度的过程,以下是对生产现场改善的详细阐述:
一、生产现场改善的目标
1、提高效率:通过优化生产流程,减少不必要的等待和停滞时间,提升生产线的整体效率。
2、降低成本:减少浪费,包括物料浪费、能源浪费、人力资源浪费等,从而降低生产成本。
3、保证质量:通过实施质量管理措施和工具,确保产品符合质量标准,减少不良品率。
4、提升安全:改善工作环境,消除安全隐患,保障员工的人身安全和健康。
5、增强灵活性:使生产系统能够快速响应市场变化和客户需求,提高生产的灵活性和适应性。
1、5S管理:整理(Seiri)、整顿(Seiton)、清扫(Seiso)、清洁(Seiketsu)、素养(Shitsuke),通过这五个步骤,建立有序、清洁、高效的工作环境。
2、流程改进:分析和优化生产流程,减少非价值添加的活动,消除瓶颈和浪费,提高生产效率,常用工具包括价值流映射、流程图等。
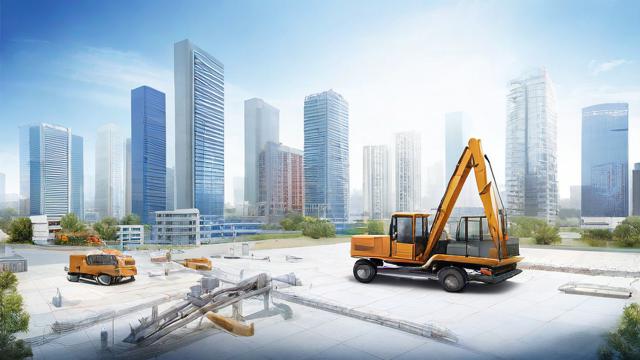
3、质量管理:建立质量管理体系,引入质量控制工具如SPC(统计过程控制)、6Sigma(六西格玛)等,提高产品质量和减少不合格品。
4、设备维护管理:通过预防性维护计划和设备管理系统,确保设备的正常运行和良好状态,减少故障停机时间。
5、人力资源管理:培训员工,提升技能水平,增强团队协作和参与度,提高员工的工作动力和责任感。
6、供应链管理:优化供应商选择,加强供应链合作,提高供应链的可靠性和透明度,降低库存成本。
7、持续改进:鼓励员工积极参与改善活动,运用PDCA循环(计划-执行-检查-行动)等工具,不断寻找问题并制定改进方案。
三、生产现场改善的实施步骤
1、现状分析:收集数据,了解当前生产现场的状况,包括生产效率、成本、质量等方面的情况。
2、目标设定:根据现状分析结果,设定具体的改善目标,明确改善的方向和重点。
3、方案设计:针对改善目标,设计具体的改善方案,包括改进措施、实施步骤、所需资源等。
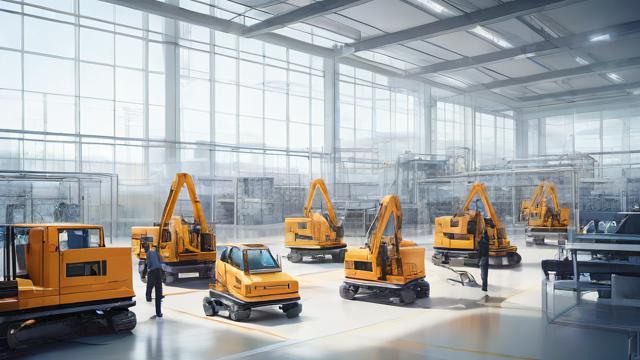
4、方案实施:按照设计方案,组织相关人员进行实施,确保改善措施得到有效执行。
5、效果评估:实施一段时间后,对改善效果进行评估,分析是否达到预期目标。
6、持续改进:根据评估结果,归纳经验教训,继续寻找新的改善机会,形成持续改进的良性循环。
四、生产现场改善的注意事项
1、领导支持:改善活动需要得到企业领导的支持和重视,才能顺利推进。
2、全员参与:鼓励全体员工积极参与改善活动,发挥每个人的智慧和创造力。
3、注重实效:改善活动应注重实际效果,避免形式主义和走过场。
4、持续学习:不断学习和借鉴先进的管理理念和方法,提升企业的管理水平和竞争力。
五、常见问题解答(FAQs)
Q1: 生产现场改善的主要障碍是什么?
A1: 生产现场改善的主要障碍包括员工抵触情绪、缺乏有效的沟通机制、资源限制以及管理层的支持不足,克服这些障碍需要建立开放透明的沟通渠道,提供必要的培训和支持,以及确保管理层的积极参与和承诺。
Q2: 如何衡量生产现场改善的效果?
A2: 衡量生产现场改善效果的指标可以包括生产效率的提升百分比、成本降低幅度、产品质量合格率的变化、交货周期的缩短以及员工满意度的提升等,通过定期收集和分析这些数据,可以客观地评估改善活动的效果,并为进一步的改进提供依据。
六、小编有话说
生产现场改善是一个持续不断的过程,它要求企业不断地审视自身的生产过程,寻找改进的空间,并付诸实践,在这个过程中,员工的参与和积极性至关重要,因为只有他们最了解自己的工作环境和存在的问题,建立一个鼓励创新、奖励改善的文化氛围是非常重要的,企业也需要不断地学习和引进新的管理理念和技术手段,以适应不断变化的市场环境和客户需求,企业才能在激烈的市场竞争中立于不败之地。