加工的浪费指的是在生产过程中,对产品或材料进行过度或不必要的加工,导致资源和能源的无效消耗。
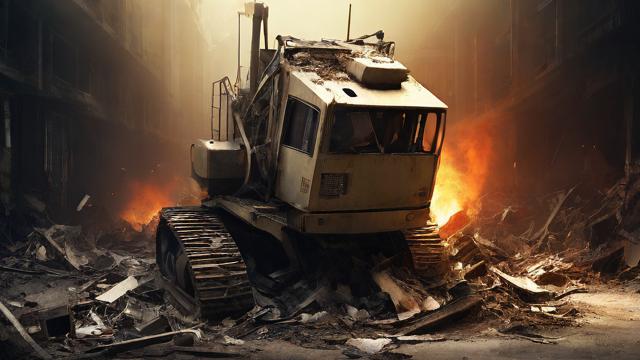
加工的浪费是精益生产中的一个重要概念,它指的是在生产过程中对产品进行超出必要范围或精度的加工活动,这种浪费不仅增加了生产成本,还可能延长生产周期,降低生产效率,加工的浪费可以分为以下几种形式:
1、质量标准过高的浪费:这是指企业为了追求产品的完美性,设定了过于严格的质量标准,导致在生产过程中需要进行超出实际需求的加工,某些部件的加工精度要求远高于客户需求,从而增加了加工难度和成本。
2、作业程序过多的浪费:这是指在生产过程中存在多余的加工步骤或动作,这些步骤或动作并不直接增加产品的价值,但却消耗了资源和时间,不必要的搬运、等待、检查等环节都可能构成加工的浪费。
3、过度加工的浪费:这是指对产品进行了超出其功能或客户需求的不必要加工,在生产过程中进行多余的打磨、抛光、装饰等,这些加工不仅消耗了额外资源,还可能降低产品的整体质量。
表现形式
超过必要以上的距离所造成的浪费:在加工过程中,如果工件需要移动过长的距离,就会造成时间和资源的浪费。
重复的试模和不必要的动作:在冲床作业上,重复的试模和不必要的动作也会增加加工时间和成本。
成型后去毛头:成型后去除毛刺的过程也是加工浪费的一种表现形式。
钻孔后的倒角浪费:钻孔后进行倒角处理,如果没有实际需求,也是一种浪费。
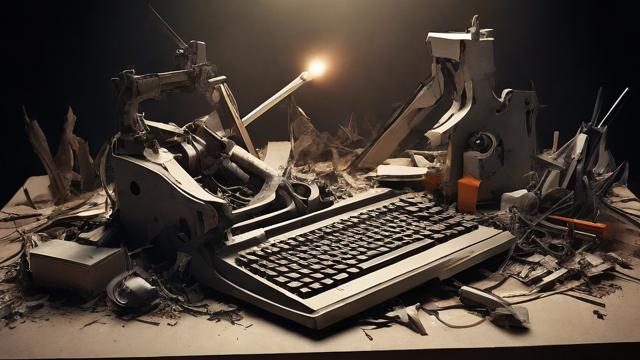
最终工序的修正动作:在最终工序中进行的修正动作,往往是由于前面工序的问题导致的,这也属于加工浪费。
原因分析
与工艺检讨不足:企业在制定生产工艺时,可能没有充分考虑到实际生产中的各种因素,导致工艺不合理。
模夹治具不良:模具和夹具的质量直接影响到加工效率和产品质量,如果模夹治具不良,就可能导致加工浪费。
标准化不彻底:缺乏标准化的生产流程和操作规范,使得员工在生产过程中难以保持一致的工作效率和质量水平。
材料未检讨:在选择材料时,如果没有充分考虑到材料的性能和成本等因素,也可能导致加工浪费。
改善对策
工程设计适正化:通过优化产品设计和工艺流程,减少不必要的加工步骤和动作。
的修正:对现有作业内容进行重新评估和调整,去除多余的加工环节。
治具改善及自働化:改进模具和夹具的设计和使用方式,提高自动化水平以减少人为操作带来的浪费。
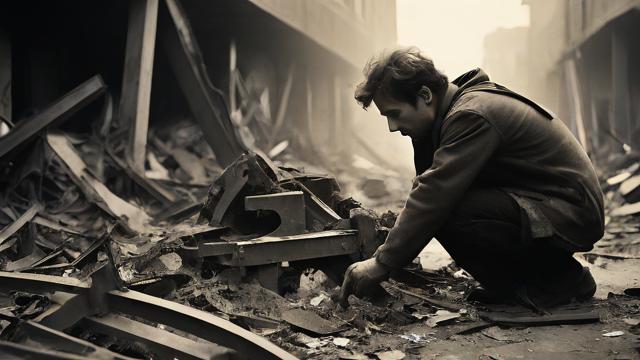
标准作业的贯彻:制定并执行标准化的生产流程和操作规范以确保生产过程的一致性和高效性。
相关问答FAQs
Q1: 如何识别加工浪费?
A1: 识别加工浪费可以通过观察生产过程中是否存在超出客户需求的加工步骤、不必要的动作、重复的试模以及最终工序的修正动作等方式进行,此外还可以通过价值流程图(VSM)等工具来揭示增值活动与非增值活动的比例从而发现潜在的加工浪费源。
Q2: 如何消除加工浪费?
A2: 消除加工浪费可以采取多种措施包括优化产品设计和工艺流程、去除多余的加工环节、改进模具和夹具的设计和使用方式、提高自动化水平以及制定并执行标准化的生产流程和操作规范等,通过这些措施可以减少不必要的资源消耗和时间浪费从而提高生产效率降低成本并提升产品质量。
小编有话说
在当今竞争激烈的市场环境中企业要想保持竞争力就必须不断寻求提高效率、降低成本的途径,而精益生产作为一种先进的管理理念和方法为企业提供了有效的解决方案,其中加工浪费作为精益生产中的重要概念之一值得我们深入理解和关注,通过识别并消除加工浪费我们可以帮助企业实现更高效的生产运作、更优质的产品质量以及更可持续的发展目标,因此让我们共同努力将精益生产的理念和方法应用到实际工作中去为企业创造更大的价值!