精益理念是一种以消除浪费、提高效率和价值为核心的管理思想,通过持续改进和团队合作来实现高效、灵活和可持续的生产方式。
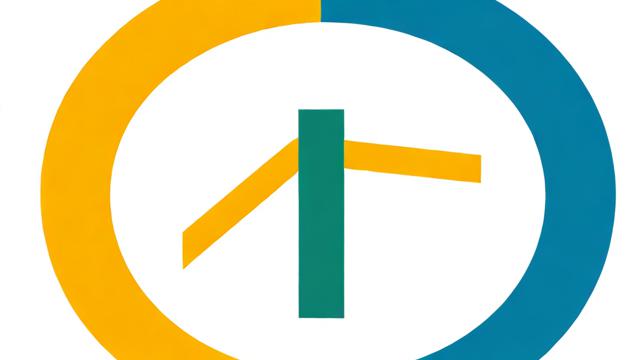
精益理念是一种源自20世纪80年代日本丰田生产方式的管理哲学,其核心思想是通过识别并消除生产和运营过程中的浪费,从而提高效率、质量和客户满意度,精益理念不仅在制造业中得到了广泛应用,还逐渐扩展到服务业、医疗保健、教育等多个领域,以下是对精益理念的详细阐述:
精益理念的核心要素
1、价值(Value):精益管理强调明确顾客需求,将焦点放在提供对顾客有价值的产品或服务上,这意味着企业需要深入了解顾客的需求和期望,以确保所生产的产品或提供的服务能够满足顾客的实际需求。
2、价值流(Value Stream):价值流是指从原材料采购到最终交付给顾客所涉及的全部过程,精益管理要求组织全面了解价值流,识别其中的瓶颈和浪费,以便进行优化。
3、流程优化(Flow):通过消除浪费和改进流程,使产品或服务的生产与交付过程更加高效顺畅,目标是实现无阻滞的价值流动,从而缩短生产周期、减少库存,提高交付速度。
4、拉动(Pull):拉动是指根据顾客需求来进行生产与供应,而非根据内部预测或批量生产,精益管理倡导「按需生产」,通过拉动机制确保只有在真正需要时才进行生产,以避免产生过剩库存和不必要的浪费。
5、消除浪费(Eliminate Waste):浪费是精益管理的敌人,其中七大浪费包括过度生产、库存、运输、过程中的等待、过度加工、不必要的动作和修正、未充分利用员工的潜力,通过消除这些浪费,组织能够更有效地利用资源。
6、人才与培训(Respect for People):精益管理强调尊重员工,认识到员工是组织最重要的资产之一,鼓励员工参与流程优化和问题解决,并提供培训和发展机会,以建设学习型组织。
精益理念的实施方法
1、标准化作业:为了确保任何一个团体或系统有效运作并持续改进,精益生产方式特推出“标准作业”制度,这有助于减少因操作不当导致的浪费和错误。
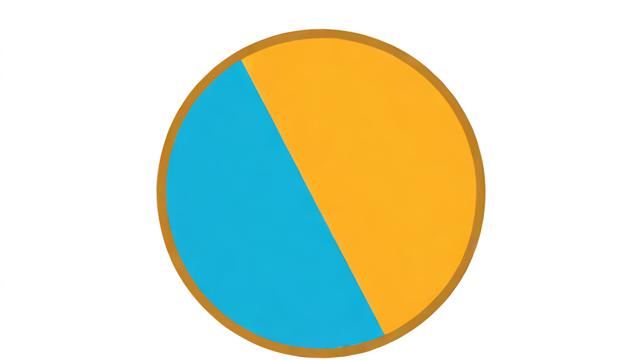
2、持续改善:精益生产方式有五项改善精神守则,包括抛弃固有的旧观念、不去找不能做的理由而去想能做的方法、学会否定现状等,通过不断的改善活动,最终实现“集小变以成大变,化不可能为可能”的目的。
3、团队协作:精益生产方式强调团队协作的重要性,通过设立“接棒区”、“自主研究会”等机制,促进团队成员之间的沟通与协作,共同解决问题。
4、现场管理:精益生产方式强调现场是一个有机体,管理部门应以“提供服务”的姿态扶持现场,并充分挖掘现场的潜能,通过实施6S管理等现场管理手段,提高现场管理的自律性和效率。
精益理念的应用效果
实施精益理念可以带来多方面的效益,它可以帮助企业降低成本、提高效率和质量;它可以增强企业的竞争力和市场响应能力;它还可以提高员工的满意度和归属感。
相关问答FAQs
Q1: 精益理念中的“浪费”具体指什么?
A1: 精益理念中的“浪费”是指一切不增加价值的活动或资源消耗,它包括七大浪费类型:过度生产、库存、运输、过程中的等待、过度加工、不必要的动作和修正、未充分利用员工的潜力。
Q2: 如何衡量精益理念的实施效果?
A2: 衡量精益理念实施效果可以从多个方面进行考量,包括但不限于生产效率的提升、成本的降低、产品质量的改善、客户满意度的提高以及员工满意度和归属感的增强,还可以通过具体的指标如生产周期时间、库存水平、废品率等来量化评估实施效果。
小编有话说
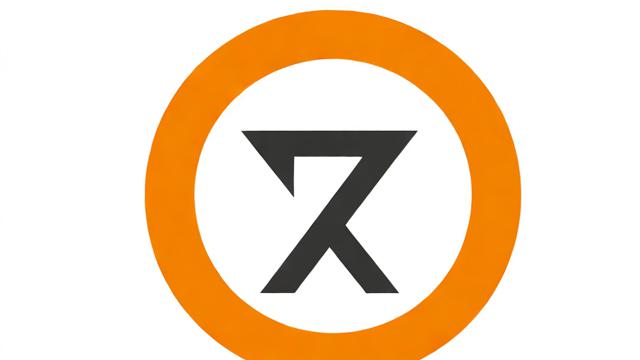
精益理念作为一种先进的管理哲学和方法体系,已经在众多企业中得到了成功应用并取得了显著成效,实施精益理念并非一蹴而就的过程,它需要企业全体员工的共同努力和持续投入,在实施过程中可能会遇到各种挑战和困难但只要我们坚定信念、持续努力就一定能够克服这些困难并取得成功,同时我们也要注意不断学习和借鉴其他企业的成功经验结合自身实际情况灵活调整实施策略以确保精益理念能够在本企业中得到有效落地和持续发展。