精益管理是一种以消除浪费、提高效率和质量为目标的管理方式,起源于日本的丰田生产方式。
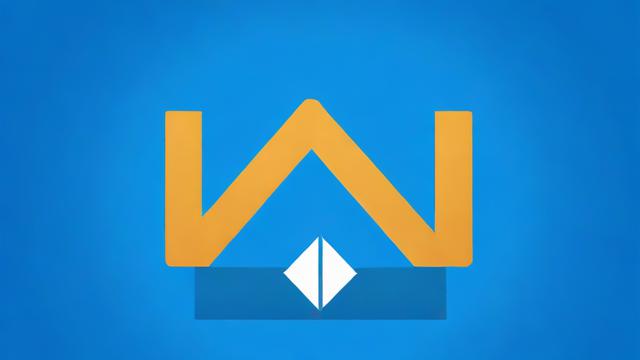
精益生产是一种旨在消除浪费、提高生产效率和产品质量的管理理念和方法,它起源于20世纪的日本丰田生产系统,由丰田汽车公司的工程师大野耐一等人发展和推广,精益生产的核心思想是通过持续改进和优化生产流程,最大限度地减少资源浪费,从而提升企业的经济效益和竞争力。
精益生产的理论基础可以追溯到多个方面,最为著名的是“七大浪费”,包括:缺陷、动作、库存、转运、过量生产、加工和等待,这些浪费被认为是生产过程中低效和不增值活动的主要来源,通过识别和消除这些浪费,企业可以实现更高的生产效率和更低的运营成本。
精益生产的特征主要包括以下几个方面:
1、准时生产(JIT):这是精益生产的核心概念之一,目的是在需要的时间生产需要的数量,避免过量生产和库存积压,这种方式不仅减少了库存成本,还提高了生产的灵活性和响应速度。
2、全员积极参与改善:精益生产强调每个员工的参与和贡献,通过提案建议制度,保障全员积极参与改善,使员工的智慧和创造力得到充分发挥,这种文化鼓励员工不断提出改进意见,推动生产过程的持续优化。
3、标准化作业:将企业中最优秀的做法固定下来,使得不同的人来做都可以达到最佳效果,标准化并不是僵化、一成不变的,标准需要不断地创新和改进,以适应市场需求的变化。
4、全面生产维护(TPM):TPM是以全员参与的方式,创建设计优良的设备系统,提高现有设备的利用率,实现安全性和高质量,防止故障发生,通过预防性维护,减少设备故障和停机时间,提高生产效率。
5、持续改进:精益生产倡导持续改进的文化,鼓励员工在生产现场提出改进意见,不断优化生产流程,通过数据分析、员工建议、现场改善等方式,企业可以发现并解决问题,不断提高生产效率和质量。
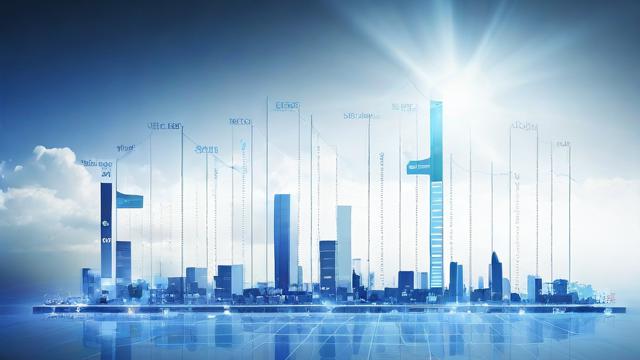
6、5S管理:5S管理(整理、整顿、清洁、清洁检查、素养)是精益生产的基础,通过实施5S管理,企业可以确保生产现场的整洁、有序,提高员工的工作效率和质量。
7、视觉管理:通过使用各种视觉工具(如看板、标识牌、颜色编码等),精益生产可以帮助员工快速识别生产状态、问题点以及改进方向,这有助于提高员工的参与度和自主管理能力。
8、拉动式生产:与传统的推动式生产不同,拉动式生产是由市场需求信息决定产品的组装,然后由产品组装来推动零件的加工,每一道工序、每一个车间分别向它的前一道工序或上游车间提出需求和工作指令,上一道工序和上游车间完全按照这些指令来进行生产,这种方式可以避免过量生产和库存积压,减少浪费。
精益生产的实施步骤通常包括以下几个方面:
1、根据客户需求重新定义价值:明确客户对产品或服务的具体需求,确定哪些活动能够为客户创造价值。
2、识别价值流并重新制定企业活动:分析当前的生产流程,识别出其中的浪费和非增值活动,重新设计流程以提高效率。
3、建立连续的作业流程:通过优化生产布局和流程,实现生产过程的连续流动,减少等待时间和瓶颈现象。
4、推行拉动式生产:采用拉动生产方式,只在需要的时候按需要的数量生产,避免过量生产和库存积压。
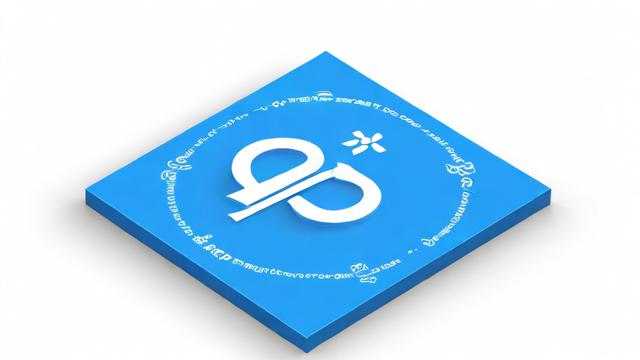
5、不断改善追求尽善尽美:建立持续改进机制,鼓励员工不断提出改进意见,推动生产过程的持续优化。
以下是关于精益生产的两个常见问题及其解答:
问:精益生产中的“第八大浪费”是什么?
答:“第八大浪费”指的是人们的创造力或主意没有被用来改进工作,即人的智慧和创造力未被充分利用,这种情况导致了低效的过程、较慢的改进速度和沮丧的人员,进而降低了盈利能力,精益生产不仅关注传统的七大浪费,还强调充分挖掘和利用人的潜力和创造力。
问:精益生产只适合生产制造部门吗?
答:不是的,精益生产不仅适用于生产制造部门,还应扩展到产品开发、协作配套、销售服务、财务管理等部门和领域,精益生产的理念和方法可以贯穿于企业生产经营活动的全过程,帮助企业全面提升效率和竞争力。
精益生产不仅是一种生产方式,更是一种管理哲学和企业文化,它要求企业在各个环节都追求精益求精,不断消除浪费,提高生产效率和产品质量,通过实施精益生产,企业可以实现更高的经济效益和更强的市场竞争力。