通过培训教育、激励机制、定期检查、持续改进和员工参与等方法,提高6S现场管理水平。
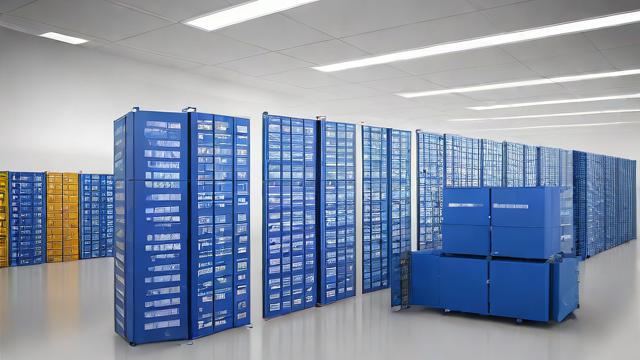
在现代企业管理中,6S现场管理是一种广泛应用的方法,旨在通过整理、整顿、清扫、清洁检查、纪律和培训六个步骤来改善工作环境和提高生产效率,除了罚款这种传统手段外,还有许多方法可以进一步提高6S现场管理水平,以下是一些具体措施:
1、制定明确的目标和计划
目标设定:在实施6S现场管理之前,首先需要制定明确的目标和计划,这些目标应该具体、可衡量,并且与组织的整体战略相一致,可以设定减少工作区域混乱程度、提高设备利用率等具体指标。
详细规划:制定详细的实施计划,包括每个步骤的时间表、责任人以及预期成果,这样可以确保6S现场管理的有序推进,并能够及时调整策略以应对可能出现的问题。
2、建立跨部门的合作机制
信息共享:6S现场管理需要各部门之间的紧密合作和协调,通过建立跨部门的合作机制,可以促进信息共享和问题解决,提高组织整体的效率和协同能力。
定期会议:定期召开跨部门会议,讨论6S现场管理的进展情况和存在的问题,共同制定解决方案,这有助于增强团队凝聚力,推动6S现场管理的持续改进。
3、培养员工的参与意识和责任感
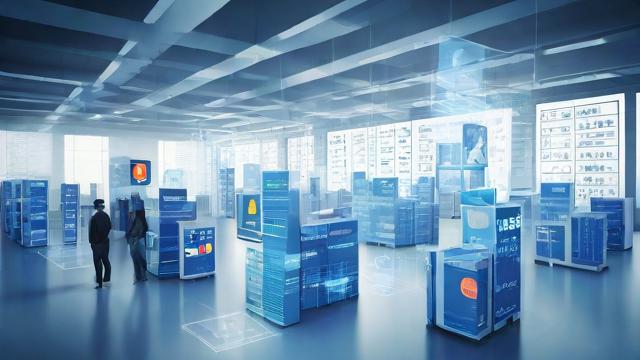
员工培训:对员工进行6S现场管理的培训,使他们了解6S现场管理的重要性和方法,掌握如何在工作中应用这些方法,培训内容可以包括整理、整顿、清扫、清洁检查、纪律和培训的具体操作方法。
激励机制:通过奖励和表彰机制,激励员工积极参与6S现场管理,可以设立“6S之星”奖项,表彰在6S现场管理中表现突出的员工。
4、建立持续改进的机制
反馈渠道:建立畅通的反馈渠道,鼓励员工提出改进建议和反馈意见,可以通过设置意见箱、开展问卷调查等方式收集员工的意见和建议。
定期评估:定期对6S现场管理的实施效果进行评估和审查,了解存在的问题和不足,及时采取措施进行改进,评估结果可以作为调整6S现场管理策略的依据。
5、利用技术手段提升管理水平
数字化工具:引入数字化工具,如物联网(IoT)设备、智能传感器等,实时监控工作环境和设备状态,及时发现问题并进行预警。
数据分析:通过数据分析,找出影响6S现场管理的关键因素,制定针对性的改进措施,分析设备故障数据,找出常见的故障模式,采取预防措施减少故障发生。
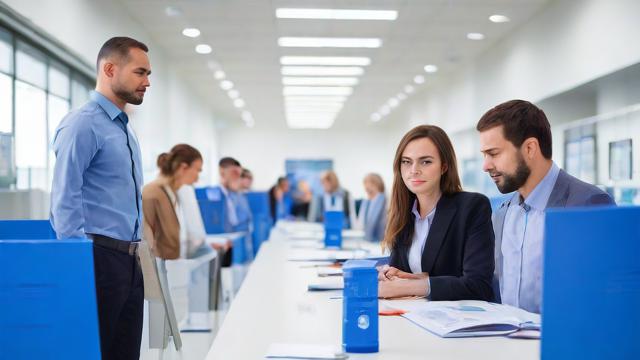
6、营造良好的企业文化
文化建设:将6S现场管理的理念融入企业文化建设中,形成全员参与的良好氛围,可以通过宣传标语、内部刊物等形式,不断强化员工对6S现场管理的认识和重视。
领导示范:管理层应以身作则,带头执行6S现场管理的各项要求,树立榜样作用,领导的支持和参与对于推动6S现场管理至关重要。
7、加强沟通与协作
内部沟通:加强各部门之间的沟通与协作,确保信息畅通无阻,可以通过定期召开协调会议、建立沟通平台等方式,促进各部门之间的信息交流和资源共享。
外部合作:与其他企业或行业组织进行交流合作,学习先进的6S现场管理经验和做法,可以通过参加行业研讨会、参观优秀企业等方式,拓宽视野,提升自身的管理水平。
8、关注细节管理
细节把控:6S现场管理强调从细节入手,注重每一个环节的管理,对工作区域的标识进行统一规范,确保标识清晰易懂;对设备进行定期维护保养,确保设备处于良好状态。
持续优化:不断优化工作流程和管理方法,消除浪费和低效环节,提高工作效率和质量。
在实施上述措施的过程中,还需注意以下几点:
持续跟进:6S现场管理是一个持续的过程,需要长期坚持和不断改进,管理层应持续跟进各项措施的执行情况,确保6S现场管理的有效实施。
灵活调整:在实施过程中,可能会遇到各种预料之外的问题和挑战,管理层应根据实际情况灵活调整策略和方法,确保6S现场管理的顺利进行。
全员参与:6S现场管理不仅仅是管理层的责任,更是全体员工的共同任务,应鼓励全体员工积极参与到6S现场管理中来,共同为企业的发展贡献力量。
除了罚款之外,还有许多方法可以提高6S现场管理水平,通过制定明确的目标和计划、建立跨部门的合作机制、培养员工的参与意识和责任感、建立持续改进的机制、利用技术手段提升管理水平、营造良好的企业文化、加强沟通与协作以及关注细节管理等措施的综合运用,可以有效提升6S现场管理水平,为企业的发展注入新的活力。