TPM(Total Productive Maintenance,全员生产维护)是一种以设备的一生为对象,追求生产系统效率极限的企业管理理念。它不仅关注设备的维修和保养,还强调通过预防管理来提高设备的综合效率和稳定性。
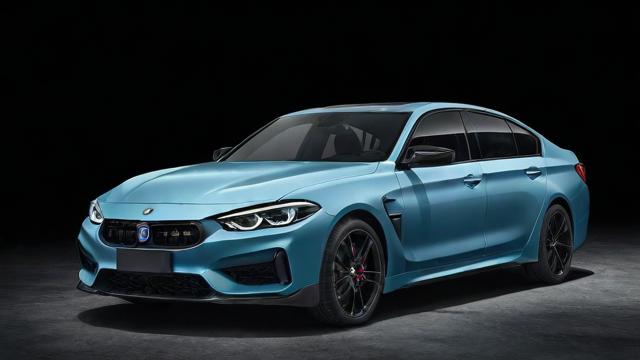
TPM(Total Productive Maintenance,全面生产维护)是一种现代设备管理和维护策略,旨在通过全员参与和系统化的维护活动,提高设备的可靠性和生产效率,降低运营成本,以下是关于TPM的详细解答:
一、TPM的定义与背景
TPM起源于日本,由日本电装公司在20世纪70年代提出,并逐渐发展成为全球制造业中广泛采用的一种设备管理方法,TPM的核心理念是“通过人的体质改善和设备的体质改善来提升企业的体质”,即通过全员参与的设备维护和管理,实现设备的高效运行和生产的持续改进。
二、TPM的核心要素
1、全员参与:TPM强调从最高管理层到一线操作员工,每个人都对设备的维护和保养负有责任,这种全员参与的模式有助于培养员工的责任感和主人翁意识,提高设备维护的效果。
2、预防性维护:TPM注重设备的预防性维护,而非仅仅依赖事后维修,通过定期的检查、清洁、润滑和调整,可以及时发现并解决潜在的设备问题,防止故障的发生。
3、自主维护:鼓励操作人员对自己的设备进行日常维护和保养,如清洁、紧固、润滑等,这有助于增强操作人员对设备的了解和熟悉程度,提高设备的使用效率和寿命。
4、计划性维护:制定详细的设备维护计划,包括定期检查、更换易损件、大修等,通过计划性维护,可以确保设备在最佳状态下运行,减少非计划停机时间。
5、持续改进:TPM是一个持续改进的过程,通过不断收集和分析设备运行数据,识别设备维护中的瓶颈和问题点,制定并实施改进措施,不断提高设备维护的效率和效果。
三、TPM的实施步骤
TPM的实施通常包括以下几个步骤:
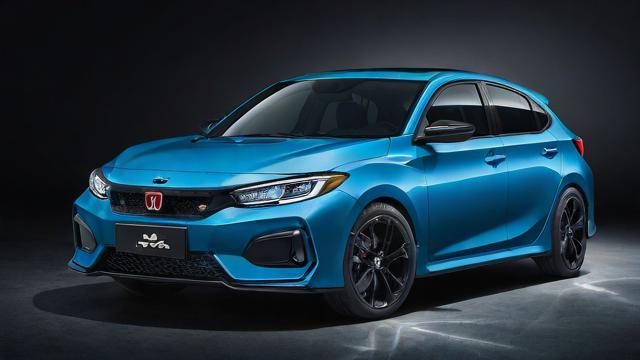
1、准备阶段:成立TPM推进组织,明确职责和分工;制定TPM实施计划和目标;开展TPM培训和宣传工作。
2、初始清洁:对设备进行全面的清洁和检查,发现并记录设备存在的问题和缺陷。
3、重复清洁:通过反复的清洁和检查活动,逐步消除设备的微缺陷和隐患,提高设备的清洁度和完好率。
4、制定基准:根据设备的清洁和检查结果,制定设备维护的基准标准和规范。
5、总点检:对设备进行全面的点检和评估,确保设备满足生产工艺的要求和标准。
6、自主维护:建立自主维护体系,鼓励操作人员对自己的设备进行日常维护和保养。
7、计划维护:制定详细的设备维护计划并严格执行,确保设备在最佳状态下运行。
8、持续改进:通过不断收集和分析设备运行数据和维护记录,识别设备维护中的瓶颈和问题点,制定并实施改进措施。
四、TPM带来的益处
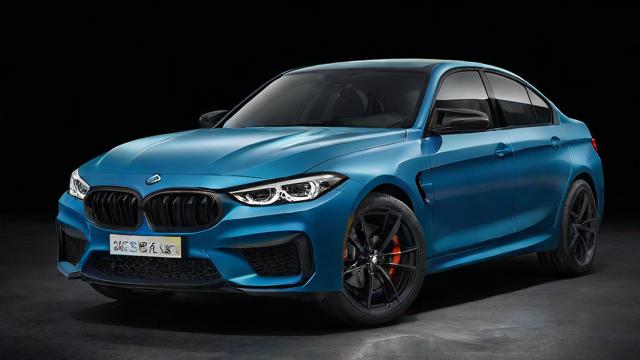
1、提高设备可靠性:通过全员参与和系统化的维护活动,减少设备故障和停机时间,提高设备的可靠性和稳定性。
2、降低运营成本:通过预防性维护和自主维护减少维修费用和备件消耗;通过提高设备使用效率降低能源消耗和生产成本。
3、提升产品质量:稳定的设备性能有助于保证生产过程的稳定性和一致性从而提高产品质量。
4、增强员工归属感:全员参与的TPM活动有助于增强员工的责任感和归属感提高员工满意度和忠诚度。
5、促进持续改进:TPM是一个持续改进的过程通过不断优化设备维护和管理流程可以不断提升企业的运营效率和竞争力。
五、TPM与其他维护策略的区别
与传统的维护策略相比,TPM更加注重全员参与和预防性维护,它不仅仅关注设备的维修和保养更强调通过提高人员素质和改善设备状况来实现企业的整体提升,此外TPM还强调持续改进的理念通过不断优化设备维护和管理流程来适应企业发展的需要。
六、FAQs
Q1: TPM与预防性维护(Preventive Maintenance, PM)有何区别?
A1: TPM与PM的主要区别在于全员参与和自主维护,PM侧重于按照预定的计划进行设备的检查、维护和修理,而TPM则强调从操作人员到管理层的全员参与,以及操作人员对自己设备的自主维护,TPM不仅关注设备的维修和保养,更注重通过提高人员素质和改善设备状况来实现企业的整体提升。
Q2: 如何衡量TPM的实施效果?
A2: TPM的实施效果可以通过多个指标来衡量,包括但不限于设备综合效率(OEE)、设备故障率、维修成本、生产效率、产品质量以及员工满意度等,通过对比实施TPM前后这些指标的变化可以直观地反映TPM的实施效果,此外还可以通过定期收集和分析设备运行数据和维护记录来评估TPM活动的执行情况和持续改进的效果。