益tpm即精益TPM,融合了精益生产的方法工具,旨在通过全员参与和全面改进提高设备效率和可靠性,实现生产过程的持续稳定。
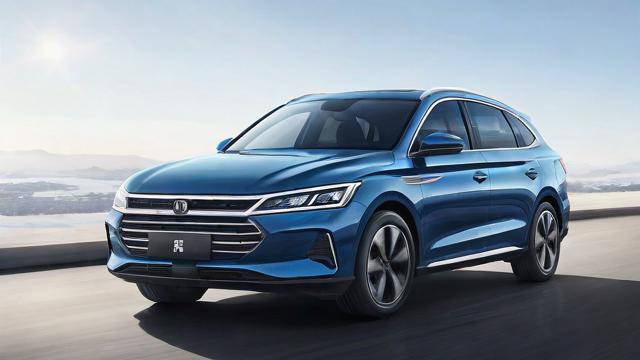
益TPM(Total Productive Maintenance)即全面生产维护,是一种旨在通过全员参与、预防性保养和持续改善来提高设备效率和可靠性的管理方法,它融合了精益生产的五大原则工具(价值流与价值流图、浪费、流动制造系统、拉动生产系统、持续改善)以及故障分析、预防性保养和设备改进等措施,以实现生产过程的稳定和持续优化。
核心理念与目标
全员参与:TPM强调所有员工对设备的维护和操作负有责任,而不仅仅是维修人员或工程师的工作,这种全员参与的理念有助于增强员工的责任感和自主性,促进团队合作和知识共享。
预防性保养:通过定期检查、清洁、润滑和更换部件等措施,减少设备故障的发生,延长设备使用寿命,预防性保养不仅降低了停机时间,还提高了生产效率和产品质量。
持续改善:TPM鼓励企业不断优化设备和工艺,通过小步快走的方式逐步改进,积累经验,提升整体竞争力,持续改善是TPM管理的核心驱动力,帮助企业实现长期可持续发展。
实施步骤与阶段
TPM的实施通常分为多个阶段,每个阶段都有明确的目标和任务,以下是TPM导入的一般步骤:
1、初期准备:建立专门的TPM团队,接受相关培训,了解TPM的基本概念和目标。
2、整理现场:对生产现场进行彻底清洁,制定并执行标准化操作规程(SOP),创造干净、有序和安全的工作环境。
3、初级保养:建立基本的设备保养计划,学习正确的保养方法,制定保养计划和检查表。
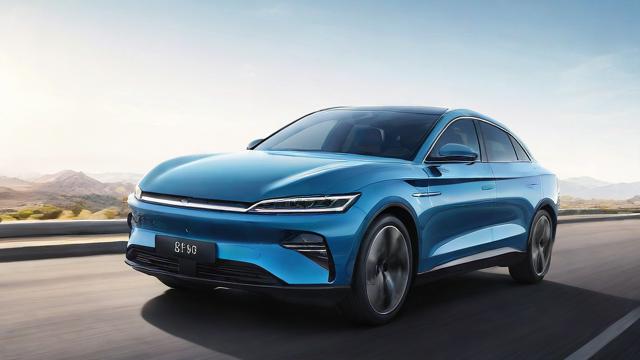
4、故障消除:分析和解决常见故障,提高设备可靠性。
5、自主保养:将设备维护的责任下放到操作人员手中,培训他们进行日常保养工作。
6、预防性维护:实施定期检查、更换关键零部件、润滑和清洁等措施。
7、教育培训:提高员工技能和知识水平,组织技术培训、安全培训和问题解决技巧培训。
8、设备可视化:安装设备监控系统,使设备状态一目了然。
9、标准化管理:制定并执行标准操作程序(SOP),监测生产效率和质量。
10、维护预防:制定维护计划,包括定期检查、润滑、校准和更换关键零部件。
11、产品质量保证:实施严格的品质控制程序,确保产品质量符合客户需求。
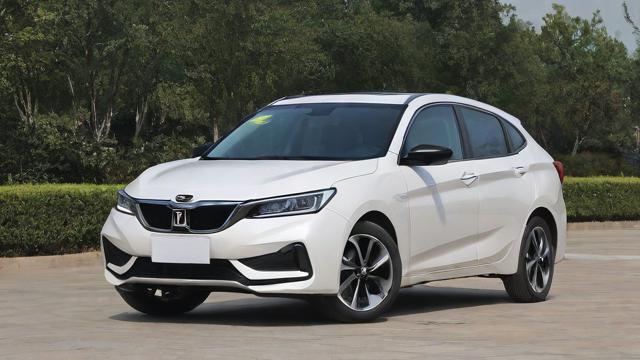
12、全员参与:鼓励所有员工积极参与TPM活动,建立共同关注设备可靠性和生产效率的企业文化。
重要性与应用
TPM在现代企业中具有重要的意义和应用价值,它不仅可以提高设备的利用率和生产效率,降低生产成本,还能增强员工技能和团队合作精神,促进企业的可持续发展,在引入精益生产之前,企业需要先实施TPM管理,以确保设备稳定可靠地运行,为后续的生产优化提供坚实的基础。
常见问题与FAQs
Q1: TPM的主要目的是什么?
A1: TPM的主要目的是通过全员参与、预防性保养和持续改善来提高设备效率和可靠性,降低生产成本,提高产品质量和生产效率。
Q2: TPM管理的核心是什么?
A2: TPM管理的核心在于全员参与和预防性保养,所有员工都对设备的维护和操作负有责任,通过日常保养、预防性维修和改善来减少设备故障发生,延长设备使用寿命。
Q3: TPM如何帮助企业提高生产效率?
A3: TPM通过降低故障率、减少停机时间和缩短生产周期来提高生产效率,它还鼓励员工参与设备改善活动,进一步提高生产力。
Q4: 实施TPM需要哪些前提条件?
A4: 实施TPM需要高层管理层的支持、跨部门成员组成的团队、明确的TPM指导方针及推进组织以及全体员工的参与和培训,还需要一个良好的设备管理体系和完善的设备维护记录。
小编有话说
TPM作为一种先进的设备管理和维护方法,已经在许多企业中得到了广泛应用并取得了显著成效,它不仅提高了设备的利用率和生产效率,还增强了员工的责任感和自主性,促进了团队合作和知识共享,实施TPM并非一蹴而就的过程,需要企业高层的支持、全员的参与和持续的努力,希望本文能够帮助读者更好地理解TPM的内涵、实施步骤及其重要性和应用价值,为企业的发展提供有益的参考和借鉴。