DFMEA设计失效模式及影响分析是一种预防性的质量工具,用于在产品设计阶段识别、评估和预防设计缺陷。
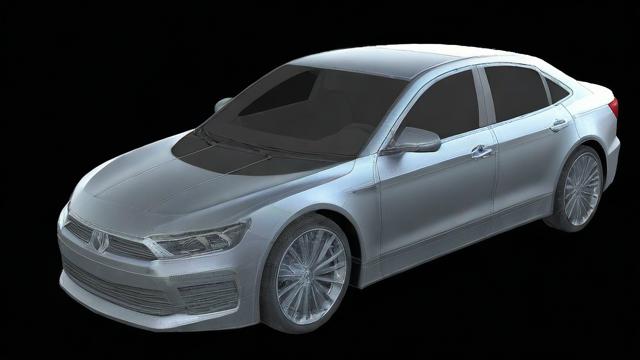
DFMEA(Design Failure Mode and Effects Analysis,设计失效模式及后果分析)是一种在产品设计阶段识别、评估和预防潜在设计缺陷的系统性方法,它通过系统地分析产品的各个组成部分及其功能,识别可能出现的失效模式,并评估这些失效对产品性能、安全性和客户满意度可能产生的影响,以下是关于DFMEA设计失效的详细回答:
DFMEA的核心概念与实施范围
1、定义与目的:
- DFMEA是一种结构化的方法,旨在通过早期识别和纠正设计缺陷来减少故障和提高产品质量。
- 它通过对产品设计的各个组成部分及其功能进行深入分析,识别可能出现的失效模式,并评估这些失效对产品性能、安全性和客户满意度可能产生的影响。
2、实施范围:
- DFMEA适用于各种产品和系统的开发阶段,包括机械、电子、软件以及综合设计项目。
- 它主要关注设计层面的风险,并强调在产品设计阶段就进行充分的分析和评估,以确保设计的可靠性。
功能分析在DFMEA中的重要性
功能分析是DFMEA的基础,它为DFMEA提供了一套逻辑框架,用于识别可能在产品生命周期中发生的潜在失效点。
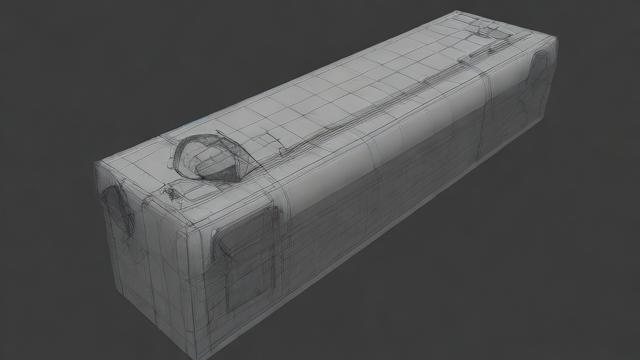
1、功能分析的基本框架:
- 识别产品或过程的功能,包括列出产品的基本功能和确定设计的目的。
- 确定功能的性能要求,详细说明功能的参数和限制。
2、功能与失效模式的关系:
- 功能的异常表现形式即为失效模式,如刹车系统的失效模式可能是“刹车响应时间过长”。
- 探讨功能不满足时可能产生的后果,如刹车扭矩不满足性能要求时可能导致的后果。
失效模式的定义及其在DFMEA中的应用
1、失效模式的基本概念:
- 失效模式描述的是产品或过程在特定条件下无法满足设计意图的状态,它揭示了问题发生的可能原因和潜在后果。
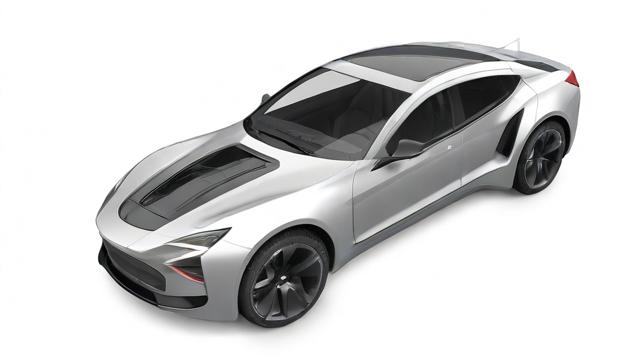
2、失效模式与产品生命周期的关系:
- 不同阶段的产品面临的风险和问题点各不相同,因此失效模式与产品生命周期紧密相关。
DFMEA的实施步骤
DFMEA的实施通常包括以下几个步骤:
1、确定分析范围:根据产品的复杂性和重要性确定分析范围,包括产品、系统、子系统或组件等。
2、识别潜在失效模式:运用头脑风暴、故障树分析等方法全面识别潜在失效模式,如机械故障、电气故障、材料故障等。
3、评估后果和严重度:对每个潜在失效模式评估其可能导致的后果和严重度,如产品性能下降、安全隐患、客户投诉等。
4、分析原因和频度:针对每个潜在失效模式分析其可能的原因和发生的频度,原因可能包括设计缺陷、材料问题、工艺问题等。
5、制定预防措施和优先级:根据后果、严重度和频度的评估结果制定相应的预防措施,并根据措施的可行性和成本效益确定优先级。
6、监控和更新:在实施预防措施后监控产品的性能和可靠性,确保措施的有效性,并及时更新DFMEA分析以应对新的失效模式或问题。
表格示例
以下是一个简化的DFMEA表格示例,用于记录和跟踪失效模式及其相关信息:
序号 | 功能描述 | 失效模式 | 失效原因 | 失效后果 | 严重度 | 频度 | RPN | 预防措施 | 重新评估 |
1 | 提供刹车系统所需的摩擦力 | 刹车响应时间过长 | 刹车片磨损 | 刹车距离增加,增加事故风险 | 高 | 中 | XXXX | 更换刹车片材质 | 是/否 |
FAQs
Q1: DFMEA与PFMEA的主要区别是什么?
A1: DFMEA主要关注的是设计阶段的潜在问题,而PFMEA则关注于生产和制造阶段的潜在问题,DFMEA多用于六西格玛设计DMADV项目中,而PFMEA多用于六西格玛DMAIC项目中。
Q2: DFMEA分析应该以什么为单位进行?
A2: DFMEA分析应该以设计责任为单位进行,对于某一“系统”/“子系统”/“零部件”,都会有两个层面的分析,顾客负责设计“系统”时要考虑“子系统”选型是否恰当,供应商则应对“子系统”继续拆解进行分析。
小编有话说
DFMEA作为一种预防性的质量工具,在产品设计的早期阶段发挥着至关重要的作用,它不仅能够帮助工程师识别潜在的设计缺陷和风险,还能够促进跨部门合作和沟通,共同解决问题,通过全面、客观、持续的DFMEA分析,我们可以发现潜在的设计问题,制定有效的预防措施,从而实现持续改进和优化,DFMEA不是一次性的任务,而是一个动态的过程,需要不断地更新和优化以适应产品设计和生产的变化。