TPM(全面生产维护)用于设备管理、生产效率提升和质量控制的各个阶段。
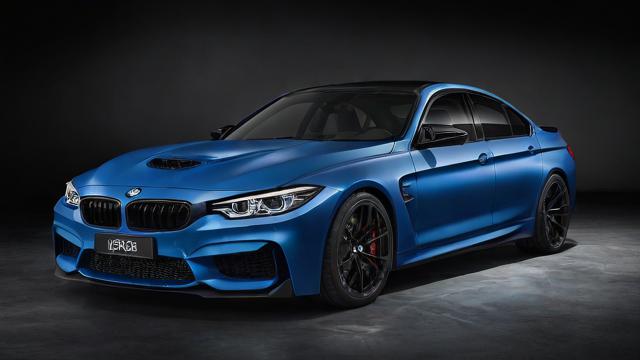
在设备管理的整个生命周期中,TPM(全面生产维护)扮演着至关重要的角色,它不仅关注设备的预防性维护,还涉及操作员的参与和持续改进,旨在减少设备故障、提高生产效率和提升产品质量,以下是TPM在不同阶段的应用:
1、初期准备
建立团队:企业需要建立一个由跨部门成员组成的TPM团队,包括生产、维修、工程和管理人员等,团队成员应接受相关培训,了解TPM的基本概念和目标。
整理现场:对生产现场进行彻底清洁,确保环境干净、有序,通过制定并执行标准化操作规程(SOP),提高员工效率和工作秩序,减少事故发生的可能性。
2、初级保养
基本保养计划:团队成员应学习如何正确进行设备保养,并制定相应的保养计划和检查表,通过实施预防性维护,可以减少设备故障率,提高设备可靠性。
故障消除:通过分析常见故障,学习如何快速识别和解决设备问题,团队成员将建立有效的故障处理机制,以确保设备能够及时恢复正常运行。
3、自主保养
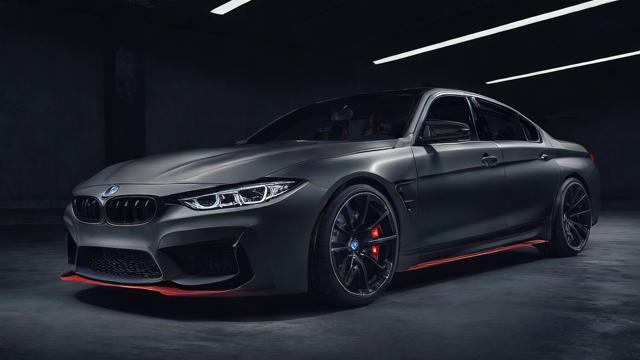
责任下放:将设备维护的责任下放到操作人员手中,操作人员将接受培训,学习如何进行日常的设备保养工作,并定期报告设备状态。
增强责任感:通过自主保养,增强操作人员对设备的责任感,提高整体生产效率。
4、故障消除
焦点改善:消除阻碍企业成长的损失要素,如设备效率损失和工作效率损失,通过焦点改善,提高企业的整体效率和竞争力。
设备管理:对设备进行专业保全,包括评价设备现状、劣化复原及弱点改善等六个阶段。
5、教育训练
技能培训:构建各岗位的技能培训认证机制,有效培训教育员工,提高工作技能,通过不断学习和提升,员工可以更好地应对日常生产中的挑战。
问题解决技巧:培训员工掌握技术问题和安全问题的解决技巧,这将有助于提高员工的综合素质和解决问题的能力。
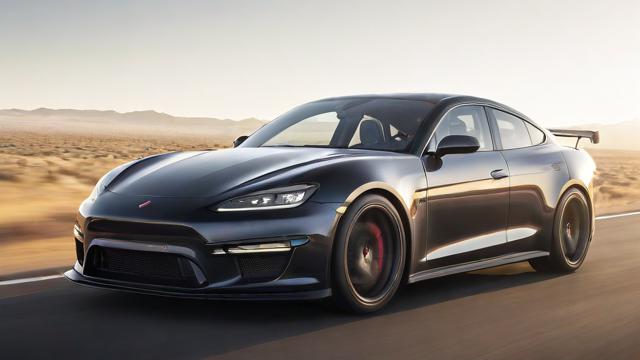
6、质量管理
质量保障:通过设备与质量的关联分析,实现零不良,开展品质控制程序,实施持续不断的改进活动,以满足客户需求。
过程监控:对生产过程进行实时监控,及时发现并解决影响产品质量的问题,通过优化生产工艺,提高产品的一致性和稳定性。
7、事务效率
间接部门效率提升:以5S活动为基础,结合改善提案、课题改善等活动,进行部门职责梳理、流程优化等效率提升活动。
人机和谐:创建人机和谐的环境,实现顾客满意、员工满意、社会满意和地球满意。
8、环境安全
安全意识提升:通过创建人机和谐的环境,提升员工的安全意识,减少事故发生的可能性。
环保措施:采取环保措施,减少生产过程中对环境的影响,实现可持续发展。
9、全员参与
激励机制:鼓励所有员工积极参与TPM导入过程,并设立奖励机制以认可和激励员工的参与。
文化建设:通过全员参与,营造一种积极的企业文化氛围,促进团队合作和持续改进。
TPM是一个系统化的管理方法,贯穿于设备管理的整个生命周期,从初期准备到全员参与,每个阶段都有其独特的作用和重要性,通过实施TPM,企业可以提高设备效率、减少停机时间、降低运营成本、提升产品质量和增强员工技能与责任感。